High-embedding essence microcapsule and preparation method thereof
A flavor microcapsule and high-package technology, which is applied in the field of high-embedded flavor microcapsules and its preparation, can solve the problems that need to be further improved, without considering the performance characteristics of wall materials, etc., and achieve excellent physical adsorption capacity, obvious anti-oxidation effect, The effect of improving the embedding performance
- Summary
- Abstract
- Description
- Claims
- Application Information
AI Technical Summary
Problems solved by technology
Method used
Examples
Embodiment 1
[0042] Add water to 50g of cornstarch to make 30% starch milk, adjust the pH of the solution to 4.5 with hydrochloric acid solution, add α-amylase with 5% starch mass, keep at 85°C for 20min, lower the temperature to 60°C, and continue to convert to DE to 11, rapidly heated to 100°C to inactivate the enzyme and stop the transformation. It is made into white fine powder by spray drying to obtain maltodextrin.
[0043] Weigh 50g of cornstarch and prepare 30% starch milk with sodium acetate buffer solution (pH=5), stir and mix in a water bath at 50°C and preheat, then add 0.5% (starch mass / mixed enzyme volume, w / v) After the mixed enzyme (α-amylase: amyloglucosidase = 1:1, volume ratio) reacted for 6 hours, the pH was adjusted to 7 with 0.5 mol / L NaOH solution. Washed, dried, sieved, porous starch.
[0044] Mix maltodextrin and porous starch at a mass ratio of 0.5:1; add distilled water and stir to form a 20% (mass ratio) solution, and add crosslinking agent at a mass ratio of ...
Embodiment 2
[0049] Add water to 100g of potato starch to make 35% starch milk, adjust the solution pH to 6.5 with hydrochloric acid solution, add α-amylase with 6% starch mass, keep at 85°C for 30min, lower the temperature to 75°C, and continue to convert to DE to 11, rapidly heated to 110°C to inactivate the enzyme and stop the conversion. It is made into white fine powder by spray drying to obtain maltodextrin.
[0050] Weigh 100g of potato starch and prepare 40% starch milk with sodium acetate buffer solution (pH=5.5), stir and mix in a water bath at 50°C and preheat, then add mixed enzyme (α-amylase: amylase) with 1% starch mass Glucosidase = 1.5:1). After reacting for 9 h, adjust the pH to 8 with 1 mol / L NaOH solution. Washed, dried, sieved, porous starch.
[0051] Mix maltodextrin and porous starch at a mass ratio of 1:1; add distilled water and stir to form a 30% (mass ratio) solution, and add crosslinking agent 3 at a ratio of 0.02% of the mass ratio of crosslinking agent to po...
Embodiment 3
[0055] Add water to 150g of pea starch to make 35% starch milk, adjust the solution pH to 6.5 with hydrochloric acid solution, add α-amylase with 7% starch mass, keep at 85°C for 40min, lower the temperature to 75°C, and continue to convert to DE to 12, rapidly heated to 120°C to inactivate the enzyme and stop the conversion. It is made into white fine powder by spray drying to obtain maltodextrin.
[0056] Weigh 150g of pea starch and prepare 45% starch milk with sodium acetate buffer solution (pH=5.5), stir and mix in a water bath at 50°C and preheat, then add mixed enzyme (α-amylase: amylase) with 1.5% starch mass Glucosidase = 1.5:1). After reacting for 12 h, adjust the pH to 7 with 1 mol / L NaOH solution. Washed, dried, sieved, porous starch.
[0057] Mix maltodextrin and porous starch at a mass ratio of 0.5:1; add a certain amount of distilled water and stir and mix to form a 30% solution, and add a crosslinking agent epoxy at a mass ratio of 0.04% between the crosslin...
PUM
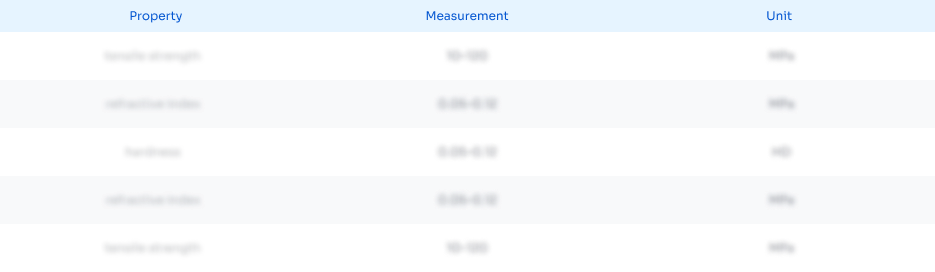
Abstract
Description
Claims
Application Information

- R&D
- Intellectual Property
- Life Sciences
- Materials
- Tech Scout
- Unparalleled Data Quality
- Higher Quality Content
- 60% Fewer Hallucinations
Browse by: Latest US Patents, China's latest patents, Technical Efficacy Thesaurus, Application Domain, Technology Topic, Popular Technical Reports.
© 2025 PatSnap. All rights reserved.Legal|Privacy policy|Modern Slavery Act Transparency Statement|Sitemap|About US| Contact US: help@patsnap.com