Tool radius directional compensation algorithm for slow slide servo turning of complex curved surface
A complex surface and tool radius technology, applied in the field of mechanical processing, can solve problems such as 'point coordinates are not easy to solve, and achieve the effect of solving solution efficiency and solution accuracy
- Summary
- Abstract
- Description
- Claims
- Application Information
AI Technical Summary
Problems solved by technology
Method used
Image
Examples
Embodiment 1
[0025] Such as figure 1 , figure 2 As shown, the present invention is used for the tool radius orientation compensation algorithm of complex curved surface slow tool servo turning, comprising the following steps:
[0026] Step 1: Establish an XZ coordinate system on the profile section curve;
[0027] Step 2: Perform point discretization on the profile section curve to obtain discrete points, and use D for the Z coordinate value i,j Indicates that i in the subscript indicates the number of times of compensation, and j indicates the point sequence; from figure 2 It can be seen from the figure that when i=0, the coordinate point is the point on the original curve without compensation, and the difference between adjacent abscissas of the original point is r / n. When i=n, it represents the final compensation point ;
[0028] Step 3: At the compensated point D 0,j , get subdivision radius compensation point D 1,j ;
[0029] Step 4: Repeat the third step above until the fi...
Embodiment 2
[0034] The first-order continuous function equation is z=0.1*cos(2πx / 10)mm, the tool radius is r=0.3mm, and the value range of x is [0,12]. The compensation error value when taking different values of n is as follows, such as image 3 As shown, when n=256, the cosine curve orientation compensation error value.
[0035] The following table shows the normal compensation error for different n values
[0036] n value 1 4 16 64 256 Compensation error(nm) 53.7 13.9 3.91 0.98 0.23
[0037] It can be seen from the above table that the maximum compensation error value is inversely proportional to n, and the algorithm has been verified.
Embodiment 3
[0039] For some types of optical complex surfaces, such as optical arrays, the cross-sectional lines of the surface often have the characteristics of first-order discontinuity, and the use of normal compensation may produce abrupt points. Figure 4 Shown as a calculation example of an equidistant offset curve family obtained by performing orientation compensation on a polyline segment, r is the offset amount, and the positive and negative values represent the offset direction. Due to the averaging effect of the algorithm, it can be seen that the sudden change points (points 1 and 3) of the original curve will form a natural smooth transition (points 2 and 4) after compensation.
PUM
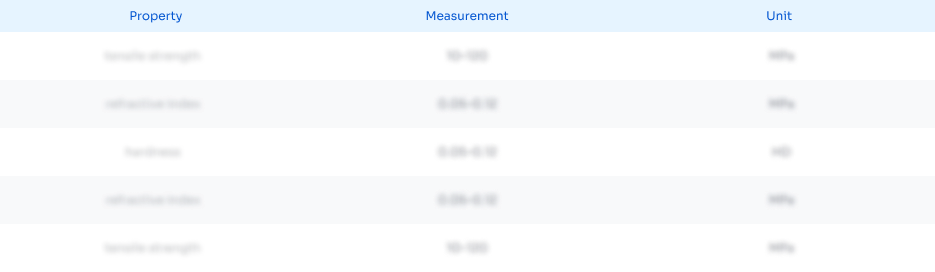
Abstract
Description
Claims
Application Information

- R&D
- Intellectual Property
- Life Sciences
- Materials
- Tech Scout
- Unparalleled Data Quality
- Higher Quality Content
- 60% Fewer Hallucinations
Browse by: Latest US Patents, China's latest patents, Technical Efficacy Thesaurus, Application Domain, Technology Topic, Popular Technical Reports.
© 2025 PatSnap. All rights reserved.Legal|Privacy policy|Modern Slavery Act Transparency Statement|Sitemap|About US| Contact US: help@patsnap.com