System and process for treating low-grade tin raw material by reducing roasting
A low-grade, batching system technology, applied in the field of tin smelting system and process, can solve the problems of large flux and vulcanization dosage, high smelting temperature and high energy consumption, achieve good energy saving and environmental protection effect, simple process configuration and good economic benefits Effect
- Summary
- Abstract
- Description
- Claims
- Application Information
AI Technical Summary
Problems solved by technology
Method used
Image
Examples
Embodiment 1
[0019] A 30-meter-long rotary kiln is used to process 50,000 tons of low-grade tin raw materials (tin ore and tin slag, etc.) containing 4%-8% tin per year, and produce tin fume products containing 35%-45% tin. Smelting and producing crude tin by the tin reduction smelting system. A secondary combustion chamber is arranged behind the rotary kiln, so that the SnO produced by the reduction roasting of the rotary kiln is oxidized to SnO in the secondary combustion chamber 2 , and then cooled by the flue gas cooling system, the SnO containing 35%-45% tin is collected in the bag filter. 2 product. The tail gas is then treated by the sulfur dioxide recovery system and discharged after reaching the standard. The slag produced by the rotary kiln contains less than 0.2% tin, and is cooled and processed by the slag cooling system, and iron is recovered by Jiaotie Smelter. Using the above-mentioned process configuration and equipment, the recovery rate of tin is greater than 95% for l...
Embodiment 2
[0021] A 44-meter-long rotary kiln is used to process 100,000 tons of low-grade tin raw materials (tin ore and tin slag, etc.) with a tin content of 3%-9% per year, and produce tin fume products with a tin content of 40%-48%. Smelting and producing crude tin by the tin reduction smelting system. A secondary combustion chamber is arranged behind the rotary kiln, so that the SnO produced by the reduction roasting of the rotary kiln is oxidized to SnO in the secondary combustion chamber 2 , and then cooled by the flue gas cooling system, the SnO containing 40%-48% tin is collected in the bag filter. 2 product. The tail gas is then treated by the sulfur dioxide recovery system and discharged after reaching the standard. The slag produced by the rotary kiln contains less than 0.2% tin, and is cooled and processed by the slag cooling system, and iron is recovered by Jiaotie Smelter. Using the above process configuration and equipment, the recovery rate of tin is greater than 93% ...
PUM
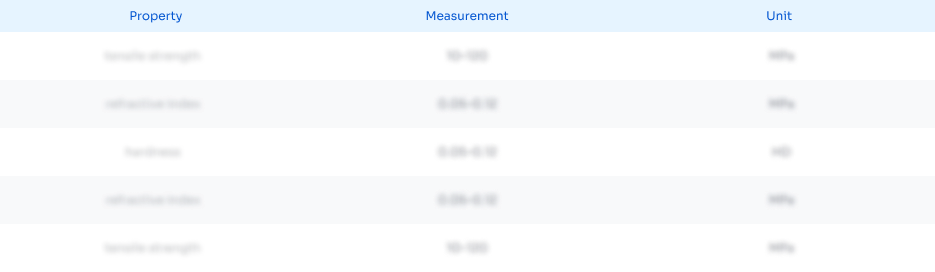
Abstract
Description
Claims
Application Information

- R&D Engineer
- R&D Manager
- IP Professional
- Industry Leading Data Capabilities
- Powerful AI technology
- Patent DNA Extraction
Browse by: Latest US Patents, China's latest patents, Technical Efficacy Thesaurus, Application Domain, Technology Topic, Popular Technical Reports.
© 2024 PatSnap. All rights reserved.Legal|Privacy policy|Modern Slavery Act Transparency Statement|Sitemap|About US| Contact US: help@patsnap.com