Lubricating oil composition, preparing method thereof and near-dry processing lubricating oil prepared from composition
A lubricating oil composition, lubricating oil technology, applied in the direction of lubricating composition, petroleum industry, etc., can solve the problem of lubrication and cooling can not be solved well, the use of lubricant is large, pollution and other problems, to achieve a significant effect of environmental protection , saving usage and prolonging the service life
- Summary
- Abstract
- Description
- Claims
- Application Information
AI Technical Summary
Problems solved by technology
Method used
Image
Examples
Embodiment 1
[0029] Step 1: Weigh 929.26g (1mol) of castor oil, 174.11 (1.5mol) of maleic acid, 2.5g of lanthanum oxide, and 3g of cerium oxide into the reaction kettle, stir and heat to 200°C, fully react for 3 hours, and discharge under reduced pressure moisture;
[0030] Step 2: When the temperature was lowered to 100° C., 1.5 g of the introduction agent lauroyl peroxide was added, and the stirring was continued to fully react for 10 hours to obtain a lubricating oil composition.
[0031] The above lubricating oil composition is applied to the TIMKEN experimental machine for repair experiments:
[0032] Add 32# mechanical oil to the oil tank of the TIMKEN experimental machine, install new rollers, turn on the motor switch, add weights continuously, and when the weights are added to 50 pounds, the motor makes a sharp noise. There is wear with a diameter of about 6 mm (longitudinal), and the wear surface is rough. Replace the mechanical oil in the oil tank with the above-mentioned lubri...
Embodiment 2
[0037] Step 1: Weigh 929.26g (1mol) of castor oil, 139.28g (1.2mol) of fumaric acid, and 1.5g of cerium oxide into the reaction kettle together, stir and heat to 180°C, fully react for 4 hours, and discharge the water under reduced pressure;
[0038] Step 2: When the temperature is lowered to 120° C., add 0.7 g of methyl ethyl ketone peroxide as an introducing agent, continue to stir and fully react for 8 hours, and a lubricating oil composition is obtained.
[0039] Weigh 100g of the lubricating oil composition prepared above, 800g of propylene glycol dicaprylate, 80g of ricinoleoyl monoethanolamine, and 20g of sodium cocoyl alanine, and mix and stir at 40°C until it becomes transparent. lubricating oil.
[0040] The preparation method of above-mentioned ricinoleoyl monoethanolamine:
[0041] Weigh 298.46 g (1 mol) of ricinoleic acid and 30.54 g (0.5 mol) of monoethanolamine into a stirrer, stir and heat to 110°C, and fully react for 1.5 hours to obtain ricinoleoyl monoethan...
Embodiment 3
[0043] Step 1: Weigh 929.26g (1mol) of castor oil, 116.07g of maleic acid (1mol) of maleic acid, and 2.5g of lanthanum oxide into the reaction kettle together, stir and heat to 190°C, fully react for 3.5 hours, and discharge the water under reduced pressure;
[0044] Step 2: When the temperature is lowered to 110° C., add 1 g of diisopropyl peroxydicarbonate as an introducing agent, continue to stir and fully react for 9 hours, and a lubricating oil composition is obtained.
[0045] Weigh 150g of the lubricating oil composition prepared above, 750g of propylene glycol dicaprylate, 60g of ricinoleoyl monoethanolamine, and 40g of sodium cocoyl alanine, mix and stir at 50°C until it becomes transparent, which is a sub-drying process lubricating oil.
[0046] The preparation method of above-mentioned ricinoleoyl monoethanolamine:
[0047] Weigh 298.46 g (1 mol) of ricinoleic acid and 61.08 g (1 mol) of monoethanolamine into a stirrer, stir and heat to 110°C, and fully react for 1...
PUM
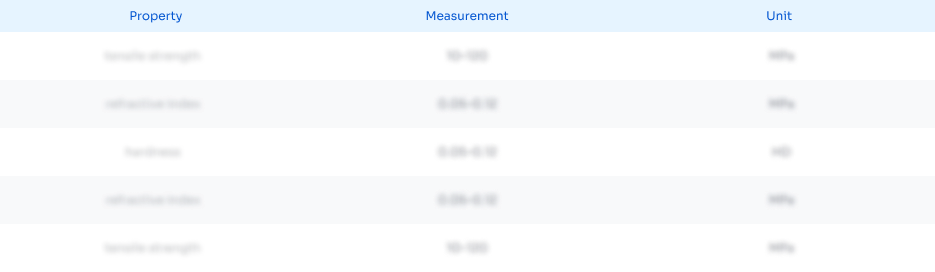
Abstract
Description
Claims
Application Information

- Generate Ideas
- Intellectual Property
- Life Sciences
- Materials
- Tech Scout
- Unparalleled Data Quality
- Higher Quality Content
- 60% Fewer Hallucinations
Browse by: Latest US Patents, China's latest patents, Technical Efficacy Thesaurus, Application Domain, Technology Topic, Popular Technical Reports.
© 2025 PatSnap. All rights reserved.Legal|Privacy policy|Modern Slavery Act Transparency Statement|Sitemap|About US| Contact US: help@patsnap.com