Carbon nitride for photocatalysis of sea water to separate out hydrogen and preparation method of carbon nitride
A carbon nitride and photocatalytic technology, applied in the field of carbon nitride, can solve the problems of enhancing photocatalytic performance, difficulty and so on
- Summary
- Abstract
- Description
- Claims
- Application Information
AI Technical Summary
Problems solved by technology
Method used
Image
Examples
Embodiment 1
[0022] 500mg CN was placed in a mortar, and a total of 0.2mL deionized water was added dropwise several times during the grinding process. After fully grinding, add 1000mg KI and grind again, and finally stack it in a corundum boat, place it in a tube furnace, and heat it to 550°C at a heating rate of 5°C / min in a nitrogen atmosphere and keep it for 2h. After the obtained samples were naturally cooled to room temperature, they were ultrasonically stirred and dispersed in deionized water. Finally, it was centrifuged and washed three times with deionized water, and dried overnight in an oven at 60°C. The dried samples were fully ground and collected for later use. The sample is named KI-CN. The same reaction conditions as in Example 1 were used for hydrogen evolution in photocatalytic deionized water, simulated seawater, Yellow Sea, and South China Sea seawater, and the 4h hydrogen evolution amounts were 11.73, 13.5, 26.27, and 28.23 μmol, respectively.
Embodiment 2
[0024] 500mg CN was placed in a mortar, and a total of 0.2mL deionized water was added dropwise several times during the grinding process. After fully grinding, add 1000mg RbI and grind again, and finally stack it in a corundum boat, place it in a tube furnace, and heat it to 550°C at a heating rate of 5°C / min in a nitrogen atmosphere and keep it for 2h. After the obtained samples were naturally cooled to room temperature, they were ultrasonically stirred and dispersed in deionized water. Finally, it was centrifuged and washed three times with deionized water, and dried overnight in an oven at 60°C. The dried samples were fully ground and collected for later use. The sample was named RbI-CN. The same reaction conditions as in Example 1 were used for hydrogen evolution in photocatalytic deionized water, simulated seawater, Yellow Sea, and South China Sea seawater, and the 4h hydrogen evolution amounts were 12.84, 20.27, 34.91, and 34.02 μmol, respectively.
Embodiment 3
[0026] 500mg CN was placed in a mortar, and a total of 0.2mL deionized water was added dropwise several times during the grinding process. After fully grinding, add 1000mg of CsI and grind again, and finally stack it in a corundum boat, place it in a tube furnace, and heat it to 550°C at a heating rate of 5°C / min in a nitrogen atmosphere and keep it for 2h. After the obtained samples were naturally cooled to room temperature, they were ultrasonically stirred and dispersed in deionized water. Finally, it was centrifuged and washed three times with deionized water, and dried overnight in an oven at 60°C. The dried samples were fully ground and collected for later use. The sample is named CsI-CN. The same reaction conditions as in Example 1 were used for hydrogen evolution in photocatalytic deionized water, simulated seawater, Yellow Sea, and South China Sea seawater, and the 4h hydrogen evolution amounts were 7.9, 33.62, 46.38, and 43.21 μmol, respectively.
PUM
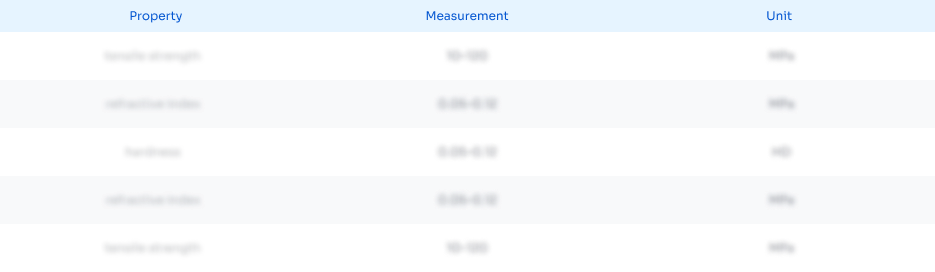
Abstract
Description
Claims
Application Information

- Generate Ideas
- Intellectual Property
- Life Sciences
- Materials
- Tech Scout
- Unparalleled Data Quality
- Higher Quality Content
- 60% Fewer Hallucinations
Browse by: Latest US Patents, China's latest patents, Technical Efficacy Thesaurus, Application Domain, Technology Topic, Popular Technical Reports.
© 2025 PatSnap. All rights reserved.Legal|Privacy policy|Modern Slavery Act Transparency Statement|Sitemap|About US| Contact US: help@patsnap.com