Coating material, coating layer, transparent back plate and preparation methods of coating material, coating layer and transparent back plate
A paint and coating technology, applied in coatings, polyurea/polyurethane coatings, photovoltaic power generation, etc., can solve the problems of increasing process difficulty and manufacturing costs, decreasing coating transparency, and not easy to disperse, etc., to achieve easy mass production , Excellent adhesion and improved adhesion
- Summary
- Abstract
- Description
- Claims
- Application Information
AI Technical Summary
Problems solved by technology
Method used
Image
Examples
Embodiment 1
[0038] (1) Add 0.2g tetraethyl orthosilicate, 0.1g KH570 to 2g deionized water and 15g ethanol, after stirring evenly, add 0.1g oxalic acid, control the stirring speed to 400rpm, stir for 1h, and then centrifuge the product, The sediment in the lower layer was removed, put into an oven for drying, the temperature of the oven was controlled at 100° C., and the drying time was 10 h.
[0039] (2) Dissolve 20g of polyester polyol (Uda Chemical) in 60g of ethyl acetate, then add 0.2g of the dried product in (1) into it, use ultrasonic to disperse evenly, and the dispersion time is 10min, then add 1g of MDI, Stir evenly, and the stirring time is 1h, then scrape-coat it on the PET substrate, and dry it at 80°C for 3h to obtain a transparent wear-resistant coating.
Embodiment 2
[0041] (1) Add 0.3g methyl orthosilicate, 0.5g KH550 to 3g deionized water and 20g methanol, stir well, add 1g formic acid, control the stirring speed to 400rpm, stir for 2h, then centrifuge the product, take the lower layer The sediment was put into an oven for drying, and the temperature of the oven was controlled at 100° C., and the drying time was 10 hours.
[0042] (2) Dissolve 30g of alkyd resin (Eternal Resin 2101-M-55) in 70g of methyl ethyl ketone, then add 0.3g of the dried product in (1) into it, use ultrasonic waves to disperse evenly, and the dispersion time is 10min, then add 5g of XDI, stirred evenly for 1 hour, then spin-coated on the PP substrate, and dried at 80°C for 3 hours to obtain a transparent wear-resistant coating.
Embodiment 3
[0044] (1) Add 0.5g tetraethyl orthosilicate, 0.1g KBM403 to 1g deionized water and 20g isopropanol, stir well, add 1g acetic acid, control the stirring speed to 400rpm, stir for 2h, and then centrifuge the product , remove the lower layer of sediment, put it into an oven for drying, control the temperature of the oven at 100° C., and the drying time for 10 hours.
[0045] (2) Dissolve 40g of polyester polyol (Uda Chemical) in 35g of butyl acetate, then add 0.5g of the dried product in (1) into it, use ultrasonic waves to disperse evenly, and the dispersion time is 10min, then add 3g of HDI, Stir evenly, and the stirring time is 1 hour, and then scrape-coat it on the PBT substrate, and dry it at 80°C for 4 hours to obtain a transparent wear-resistant coating.
PUM
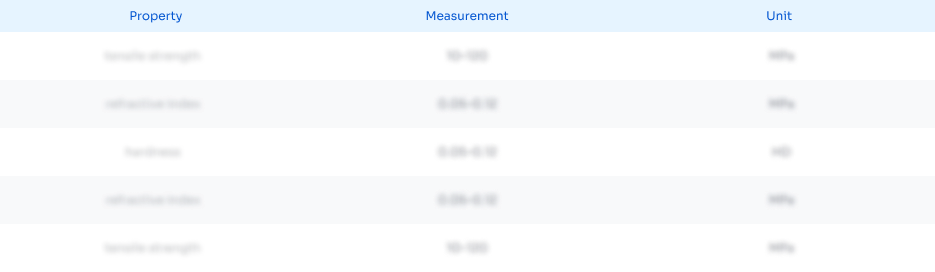
Abstract
Description
Claims
Application Information

- R&D Engineer
- R&D Manager
- IP Professional
- Industry Leading Data Capabilities
- Powerful AI technology
- Patent DNA Extraction
Browse by: Latest US Patents, China's latest patents, Technical Efficacy Thesaurus, Application Domain, Technology Topic, Popular Technical Reports.
© 2024 PatSnap. All rights reserved.Legal|Privacy policy|Modern Slavery Act Transparency Statement|Sitemap|About US| Contact US: help@patsnap.com