Preparation method of high efficient oil storage type oil absorbent felt material
An oil-absorbing felt and high-efficiency technology, which is applied in the field of preparation of high-efficiency oil-storage-type oil-absorbing felt materials, can solve problems such as poor oil absorption effect and oil storage effect, and achieve improved oil absorption and oil storage performance, stable structure, and increased internal oil absorption. Effect
- Summary
- Abstract
- Description
- Claims
- Application Information
AI Technical Summary
Problems solved by technology
Method used
Examples
preparation example Construction
[0029] Preparation of treated chitosan: Mix chitosan with a deacetylation degree of 90% and acetic acid solution with a mass fraction of 5% according to a mass ratio of 1:20~30, and stir magnetically at 500~800r / min for 35~60min. To obtain the chitosan solution, take the chitosan solution and add nano-TiO at a mass ratio of 18~30:1 2Mix, move to an ultrasonic oscillator and disperse ultrasonically at a frequency of 50~65kHz for 12~20min to obtain a dispersion. Take the dispersion and add stearic acid at a mass ratio of 20~30:1 to mix, and stir magnetically at 600~900r / min for 2~4h , vacuumize for 1~3h, filter with suction, take the filter residue and wash it with absolute ethanol for 2~4 times, then move it to a 65~80°C oven and dry it for 3~5h to obtain the processed chitosan.
[0030] Plasticizer: Mix triethyl citrate and dioctyl phthalate at a mass ratio of 4-8:1 to obtain a plasticizer.
[0031] Antioxidant: Mix tert-butylhydroquinone and alkylated diphenylamine at a mass...
Embodiment 1
[0039] Mixed lotion: Mix absolute ethanol and acetone at a volume ratio of 6:1 to obtain a mixed lotion.
[0040] Reagent A: Mix 20% NaOH solution and sodium carbonate at a mass ratio of 7:1 to obtain Reagent A.
[0041] Reagent B: Mix ethyl bromide and toluene at a mass ratio of 8:1 to obtain reagent B.
[0042] Excipients: Zinc stearate and lauryl dimethyl betaine are mixed according to the mass ratio of 1:3 to obtain the excipients.
[0043] Ball milling medium: Mix absolute ethanol and glycerin at a mass ratio of 5:1 to obtain a ball milling medium.
[0044] Preparation of chitosan treated product: mix chitosan with a deacetylation degree of 90% and acetic acid solution with a mass fraction of 5% according to a mass ratio of 1:20, and stir magnetically at 500r / min for 35min to obtain a chitosan liquid. Take the chitosan solution and add nano-TiO at a mass ratio of 18:1 2 Mix, move to an ultrasonic oscillator and disperse ultrasonically at a frequency of 50kHz for 12min ...
Embodiment 2
[0054] Mixed lotion: Mix absolute ethanol and acetone at a volume ratio of 10:1 to obtain a mixed lotion.
[0055] Reagent A: Mix 20% NaOH solution and sodium carbonate at a mass ratio of 12:1 to obtain Reagent A.
[0056] Reagent B: Mix ethyl bromide and toluene at a mass ratio of 8:3 to obtain reagent B.
[0057] Excipients: Zinc stearate and lauryl dimethyl betaine are mixed according to the mass ratio of 1:7 to obtain the excipients.
[0058] Ball milling medium: Mix absolute ethanol and glycerin at a mass ratio of 8:1 to obtain a ball milling medium.
[0059] Preparation of chitosan treated product: mix chitosan with a deacetylation degree of 90% and acetic acid solution with a mass fraction of 5% according to a mass ratio of 1:30, and stir magnetically at 800r / min for 60min to obtain a chitosan liquid. Take chitosan solution and add nano-TiO at a mass ratio of 30:1 2 Mix, move to an ultrasonic oscillator and disperse ultrasonically at a frequency of 65kHz for 20min to...
PUM
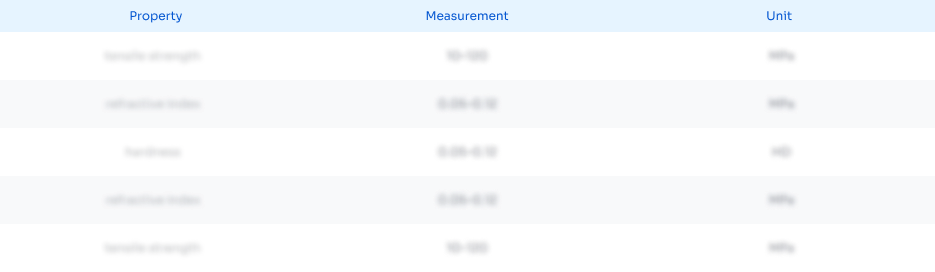
Abstract
Description
Claims
Application Information

- Generate Ideas
- Intellectual Property
- Life Sciences
- Materials
- Tech Scout
- Unparalleled Data Quality
- Higher Quality Content
- 60% Fewer Hallucinations
Browse by: Latest US Patents, China's latest patents, Technical Efficacy Thesaurus, Application Domain, Technology Topic, Popular Technical Reports.
© 2025 PatSnap. All rights reserved.Legal|Privacy policy|Modern Slavery Act Transparency Statement|Sitemap|About US| Contact US: help@patsnap.com