Method for carrying out half-in-site observation on initiation position of point corrosion pit
An in-situ, pitting corrosion technology, applied in the field of austenitic-ferritic duplex stainless steel, can solve the problems of unclear G-phase and α effects, inability to determine the location of nano-scale pitting pit initiation, etc. high degree of effect
- Summary
- Abstract
- Description
- Claims
- Application Information
AI Technical Summary
Problems solved by technology
Method used
Image
Examples
Embodiment 1
[0031] The Z3CN20.09M stainless steel heat-aged at 475°C for 2000 hours was cut into 15mm×15mm×5mm specimens, which were ground and polished. Put in 6wt.% FeCl at 35°C 3 After soaking in acid solution for 24 hours, the samples were taken out and subjected to ultrasonic pickling treatment immediately, and the corrosion morphology was observed under a metallographic microscope. It can be seen that the location of corrosion is mainly concentrated in the ferrite.
[0032] Cut the Z3CN20.09M stainless steel sample heat-aged at 475°C for 2000 hours into 0.5mm thick slices, grind it with 600#, 1200#, 2000# metallographic sandpaper in turn to 60-100μm and punch into a 3mm diameter disc. Then use 2000# metallographic sandpaper to polish to below 50μm thickness. The polished sample was initially thinned in an electrolytic double-spray apparatus, and the electrolyte was 95% ethanol + 5% perchloric acid, and then the ion thinning apparatus was used to finally thin it into a transmission...
Embodiment 2
[0038] The Z3CN20.09M stainless steel heat-aged at 475°C for 2000 hours was cut into 15mm×15mm×5mm specimens, which were ground and polished. Put in 6wt.% FeCl at 35°C 3 After soaking in acid solution for 24 hours, the samples were taken out and subjected to ultrasonic pickling treatment immediately, and the corrosion morphology was observed under a metallographic microscope. It can be seen that the location of corrosion is mainly concentrated in the ferrite.
[0039] Cut the Z3CN20.09M stainless steel sample heat-aged at 475°C for 2000 hours into 0.5mm thick slices, grind them to 60-100μm with 600#, 1200#, and 2000# metallographic sandpaper in turn, and punch them into discs with a diameter of 3mm. Then use 2000# metallographic sandpaper to polish to below 50μm thickness. The polished sample was initially thinned in an electrolytic double-spray apparatus, and the electrolyte was 95% ethanol + 5% perchloric acid, and then the ion thinning apparatus was used to finally thin i...
Embodiment 3
[0045]The Z3CN20.09M stainless steel heat-aged at 475°C for 3000 hours was cut into 15mm×15mm×5mm specimens, which were ground and polished. Put in 6wt.% FeCl at 35°C 3 After soaking in acid solution for 24 hours, the samples were taken out and subjected to ultrasonic pickling treatment immediately, and the corrosion morphology was observed under a metallographic microscope. It can be seen that the location of corrosion is mainly concentrated in the ferrite.
[0046] The Z3CN20.09M stainless steel sample that was heat-aged at 475°C for 3000 hours was cut into 0.5mm thick slices, polished with 600#, 1200#, 2000# metallographic sandpaper to 60-100μm in turn and punched into a 3mm diameter disc. Then use 2000# metallographic sandpaper to polish to below 50μm thickness. The polished sample was initially thinned in an electrolytic double-spray apparatus, and the electrolyte was 95% ethanol + 5% perchloric acid, and then the ion thinning apparatus was used to finally thin it into ...
PUM
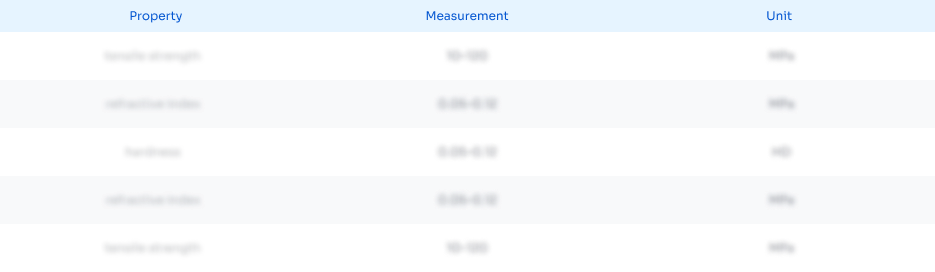
Abstract
Description
Claims
Application Information

- R&D
- Intellectual Property
- Life Sciences
- Materials
- Tech Scout
- Unparalleled Data Quality
- Higher Quality Content
- 60% Fewer Hallucinations
Browse by: Latest US Patents, China's latest patents, Technical Efficacy Thesaurus, Application Domain, Technology Topic, Popular Technical Reports.
© 2025 PatSnap. All rights reserved.Legal|Privacy policy|Modern Slavery Act Transparency Statement|Sitemap|About US| Contact US: help@patsnap.com