A kind of preparation method of surface-modified graphite microflake waterborne epoxy resin anticorrosion coating
A technology of water-based epoxy resin and graphite microchips, which is applied in the direction of epoxy resin coatings, anti-corrosion coatings, polyester coatings, etc., can solve the problems of poor anti-corrosion effect, and achieve the characteristics of not easy to pulverize, increase adhesion, and good weather resistance Effect
- Summary
- Abstract
- Description
- Claims
- Application Information
AI Technical Summary
Problems solved by technology
Method used
Image
Examples
Embodiment 1
[0022] A preparation method for surface-modified graphite microflake waterborne epoxy resin anticorrosion coating, comprising the following steps:
[0023] 1) Preparation of graphite oxide powder: immerse 10g of ground graphite powder in 200ml of concentrated nitric acid, soak for 1h at 0°C, cool down to -15°C, add 1ml of concentrated phosphoric acid and 40g of potassium ferrate, react at 60°C for 0.5h and then centrifuge , washing the filter cake with deionized water until the pH of the washing solution is 6-7, placing it in a vacuum drying oven, and drying at 60°C for 6 hours to obtain graphite oxide powder;
[0024] 2) prepare the graphite oxide powder of hydroxyl group and carboxyl group: the graphite oxide powder containing NaBH 4 and CaCl 2 Soak in the solution for 10 hours and then filter, wash the filter cake with deionized water and dry it in a drying oven at 60°C for 6 hours to obtain multilayer graphite powder containing hydroxyl and carboxyl groups;
[0025] 3) P...
Embodiment 2
[0030] A preparation method for surface-modified graphite microflake waterborne epoxy resin anticorrosion coating, comprising the following steps:
[0031] 1) Preparation of graphite oxide powder: immerse 10g of ground graphite powder in 200ml of concentrated nitric acid, soak for 1.5h at 0°C, cool down to -15°C, add 1ml of concentrated phosphoric acid and 40g of potassium ferrate, react at 25°C for 12h and then centrifuge , washing the filter cake with deionized water until the pH of the washing solution is 6-7, placing it in a vacuum drying oven, and drying at 65°C for 5 hours to obtain graphite oxide powder;
[0032]2) prepare the graphite oxide powder of hydroxyl group and carboxyl group: the graphite oxide powder containing NaBH 4 and CaCl 2 Soak in the solution for 9 hours and then filter, wash the filter cake with deionized water and dry it in a drying oven at 60°C for 6 hours to obtain a multilayer graphite powder containing hydroxyl and carboxyl groups;
[0033] 3) ...
Embodiment 3
[0038] A preparation method for surface-modified graphite microflake waterborne epoxy resin anticorrosion coating, comprising the following steps:
[0039] 1) Preparation of graphite oxide powder: immerse 10g of ground graphite powder in 200ml of concentrated nitric acid, soak at 0°C for 2h, cool down to -15°C, add 1ml of concentrated phosphoric acid and 40g of potassium ferrate, react at -10°C for 24h and then centrifuge , washing the filter cake with deionized water until the pH of the washing solution is 6-7, placing it in a vacuum drying oven, and drying at 70°C for 4 hours to obtain graphite oxide powder;
[0040] 2) prepare the graphite oxide powder of hydroxyl group and carboxyl group: the graphite oxide powder containing NaBH 4 and CaCl 2 Soak in the solution for 10 hours and then filter, wash the filter cake with deionized water and dry it in a drying oven at 60°C for 6 hours to obtain multilayer graphite powder containing hydroxyl and carboxyl groups;
[0041] 3) P...
PUM
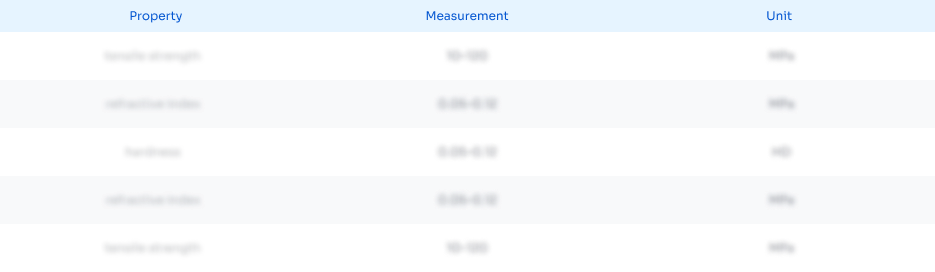
Abstract
Description
Claims
Application Information

- R&D Engineer
- R&D Manager
- IP Professional
- Industry Leading Data Capabilities
- Powerful AI technology
- Patent DNA Extraction
Browse by: Latest US Patents, China's latest patents, Technical Efficacy Thesaurus, Application Domain, Technology Topic, Popular Technical Reports.
© 2024 PatSnap. All rights reserved.Legal|Privacy policy|Modern Slavery Act Transparency Statement|Sitemap|About US| Contact US: help@patsnap.com