Composite membrane for mabr and preparation method thereof
A composite membrane and fiber membrane technology, applied in the field of MABR composite membrane, can solve the problems of gas flux decline, low oxygen flux, and hydrophobic performance decline.
- Summary
- Abstract
- Description
- Claims
- Application Information
AI Technical Summary
Problems solved by technology
Method used
Image
Examples
Embodiment 1
[0023] A composite membrane for MABR proposed by the present invention includes a composite hollow fiber membrane and multi-dimensional holes arranged on the composite hollow fiber membrane;
[0024] Its preparation method comprises the following steps:
[0025] S1: Put the polyvinylidene fluoride raw material and the 5% diluent of the polyvinylidene fluoride raw material in the reaction kettle, and melt at a high temperature at the same time, and control the heating temperature at 120°C;
[0026] S2: After complete melting, keep the temperature of the reactor at 60°C, stand in the reactor for defoaming, and start spinning after standing for 3 hours;
[0027] S3: Under the traction of the take-up wheel, the spun membrane filaments are extracted into the 70% mass ratio of polyvinylidene fluoride raw materials for extraction, the take-up speed is 400m / min, the cooling temperature is 30°C, and phase separation occurs during cooling The phenomenon forms pores, and the composite m...
Embodiment 2
[0031] A composite membrane for MABR proposed by the present invention includes a composite hollow fiber membrane and multi-dimensional holes arranged on the composite hollow fiber membrane;
[0032] Its preparation method comprises the following steps:
[0033] S1: Put the polyvinylidene fluoride raw material and the 5% diluent of the polyvinylidene fluoride raw material in the reaction kettle, and melt at a high temperature at the same time, and control the heating temperature at 130°C;
[0034] S2: After complete melting, keep the temperature of the reactor at 65°C, stand in the reactor for defoaming, and start spinning after standing for 3.5 hours;
[0035] S3: Under the traction of the take-up wheel, the spun film filaments are extracted into the 70% mass ratio of polyvinylidene fluoride raw material extraction solution, the take-up speed is 450m / min, the cooling temperature is 35°C, and phase separation occurs after cooling The phenomenon forms pores, and the composite ...
Embodiment 3
[0039] A composite membrane for MABR proposed by the present invention includes a composite hollow fiber membrane and multi-dimensional holes arranged on the composite hollow fiber membrane;
[0040] Its preparation method comprises the following steps:
[0041] S1: Put the polyvinylidene fluoride raw material and the 5% diluent of the polyvinylidene fluoride raw material in the reaction kettle, and melt at a high temperature at the same time, and control the heating temperature at 150°C;
[0042] S2: After complete melting, keep the temperature of the reactor at 70°C, stand in the reactor for defoaming, and start spinning after standing for 4 hours;
[0043] S3: Under the traction of the take-up wheel, the spun film filaments are extracted into the 70% mass ratio of polyvinylidene fluoride raw materials for extraction, the take-up speed is 500m / min, the cooling temperature is 45°C, and phase separation occurs during cooling The phenomenon forms pores, and the composite membr...
PUM
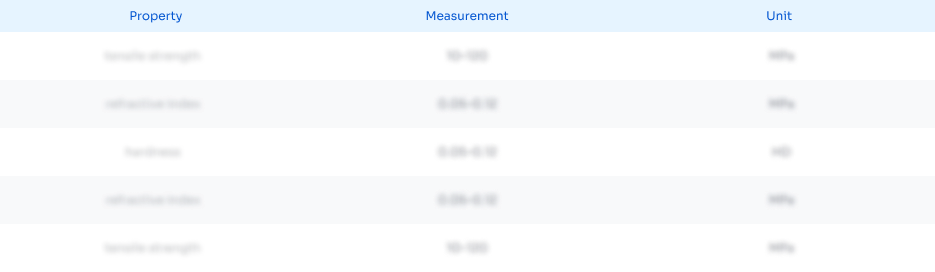
Abstract
Description
Claims
Application Information

- R&D
- Intellectual Property
- Life Sciences
- Materials
- Tech Scout
- Unparalleled Data Quality
- Higher Quality Content
- 60% Fewer Hallucinations
Browse by: Latest US Patents, China's latest patents, Technical Efficacy Thesaurus, Application Domain, Technology Topic, Popular Technical Reports.
© 2025 PatSnap. All rights reserved.Legal|Privacy policy|Modern Slavery Act Transparency Statement|Sitemap|About US| Contact US: help@patsnap.com