A simulation device and method for the heating process of molten steel in the nozzle channel
A heating device and simulation method technology, applied in the direction of material thermal development, material resistance, etc., to achieve the effects of small heat loss, easy and accurate control, and high heat conduction efficiency
- Summary
- Abstract
- Description
- Claims
- Application Information
AI Technical Summary
Problems solved by technology
Method used
Image
Examples
Embodiment 1
[0031] A simulation device for the heating process of molten steel in a nozzle channel, comprising a ladle model, a tundish model, an aluminum shroud, a heating device, a conductivity monitoring device, a temperature monitoring device, and a tracer adding device. The ladle model is Above the tundish model, the aluminum shroud is installed at the bottom of the ladle model according to the actual positional relationship between the ladle and the shroud, the heating device is installed at the aluminum shroud, the ladle model, the aluminum shroud and the middle The dimensions of the ladle model are all scaled down with reference to the actual ladle, shroud and tundish sizes according to similar principles. The tracer adding device is set above the aluminum shroud, and the tundish model has a water outlet. The conductivity monitoring device is located at the outlet.
[0032] A method for simulating the heating process of molten steel in a nozzle channel, using the aforementioned simul...
Embodiment 2
[0040] A simulation device for the heating process of molten steel in a nozzle channel, including a ladle model, a tundish model, a copper shroud, a heating device, a conductivity monitoring device, a temperature monitoring device, and a tracer adding device. The ladle model is Above the tundish model, the copper shroud is installed at the bottom of the ladle model according to the actual positional relationship between the ladle and the shroud, the heating device is installed at the copper shroud, the ladle model, the copper shroud and the middle The size of the ladle model is all scaled down with reference to the actual ladle, shroud and tundish sizes according to similar principles. The tracer adding device is set above the copper shroud, and the tundish model has a water outlet. The conductivity monitoring device is located at the outlet, and the heating device includes a heat-conducting water tank, a constant-temperature water tank, and a water pump, and the heat-conducting...
Embodiment 3
[0049] A simulation device for the heating process of molten steel in a nozzle channel, comprising a ladle model, a tundish model, an aluminum shroud, a heating device, a conductivity monitoring device, a temperature monitoring device, and a adding device, the ladle model is in the middle Above the ladle model, the aluminum shroud is installed at the bottom of the ladle model according to the actual positional relationship between the ladle and the shroud, the heating device is installed at the aluminum shroud, the size of the ladle model, the aluminum shroud and the tundish model The dimensions of the ladle, shroud and tundish are all reduced in proportion to the actual ladle, shroud and tundish according to similar principles. The tracer adding device is arranged above the aluminum shroud. The tundish model has three outlets. The conductivity The monitoring device is located at the outlet, and the heating device includes a heat-conducting water tank, a constant-temperature wat...
PUM
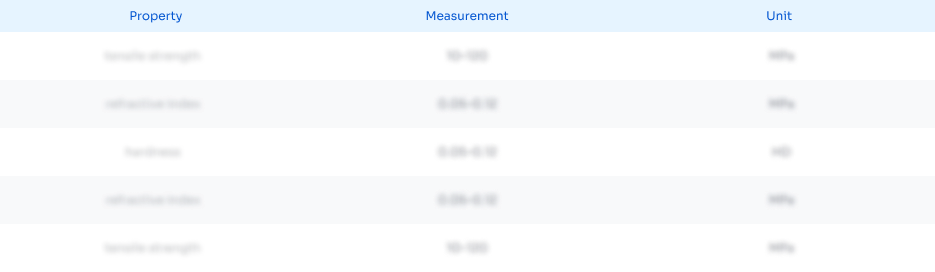
Abstract
Description
Claims
Application Information

- Generate Ideas
- Intellectual Property
- Life Sciences
- Materials
- Tech Scout
- Unparalleled Data Quality
- Higher Quality Content
- 60% Fewer Hallucinations
Browse by: Latest US Patents, China's latest patents, Technical Efficacy Thesaurus, Application Domain, Technology Topic, Popular Technical Reports.
© 2025 PatSnap. All rights reserved.Legal|Privacy policy|Modern Slavery Act Transparency Statement|Sitemap|About US| Contact US: help@patsnap.com