High-sulfur tail gas treatment system and technology
A tail gas treatment and high-sulfur technology, applied in the chemical industry, can solve the problems of low-temperature acid dew point corrosion of heat exchange equipment, low waste heat utilization rate, poor incineration effect, etc., to avoid low-temperature acid dew point corrosion, avoid acid dew point corrosion, Guarantee the effect of long-term stable operation
- Summary
- Abstract
- Description
- Claims
- Application Information
AI Technical Summary
Problems solved by technology
Method used
Image
Examples
Embodiment 1
[0037] Such as figure 1 As shown, this embodiment provides a high-sulfur tail gas treatment system, including a tail gas incineration unit and a flue gas waste heat recovery unit. The tail gas incineration unit includes a burner 1 and an incinerator 2. The burner 1 and the incinerator 2 are connected through a flange or Welding type connection, the mixture of high-sulfur tail gas, fuel gas and combustion-supporting air passes through the incinerator 2 and then discharges high-temperature flue gas into the flue gas waste heat recovery unit. The flue gas waste heat recovery unit is set as multi-stage waste heat recovery equipment, including Pressurized steam superheater 3, steam generator 4, energy-saving heat exchange equipment 5, air preheater 6, combustion-supporting fan 7, etc. The fuel gas source 14 is connected to the burner, the fuel gas passes through the burner 1 and then enters the furnace for supplementary combustion, the steam superheater 3 is connected to the incine...
Embodiment 2
[0063] Such as figure 2 As shown, this embodiment provides a high-sulfur tail gas treatment system, including a tail gas incineration unit and a flue gas waste heat recovery unit. The tail gas incineration unit includes a burner 1 and an incinerator 2. The burner 1 and the incinerator 2 are connected through a flange or Welding type connection, the mixture of high-sulfur tail gas, fuel gas and combustion-supporting air passes through the incinerator 2 and then discharges high-temperature flue gas into the flue gas waste heat recovery unit. The flue gas waste heat recovery unit is set as multi-stage waste heat recovery equipment, including Pressurized steam superheater 3, steam generator 4, energy-saving heat exchange equipment, air preheater 6, combustion-supporting fan 7, etc. The fuel gas source 14 is connected to the burner, the fuel gas passes through the burner 1 and enters the furnace for combustion, the steam superheater 3 is connected to the incinerator 2, the steam g...
PUM
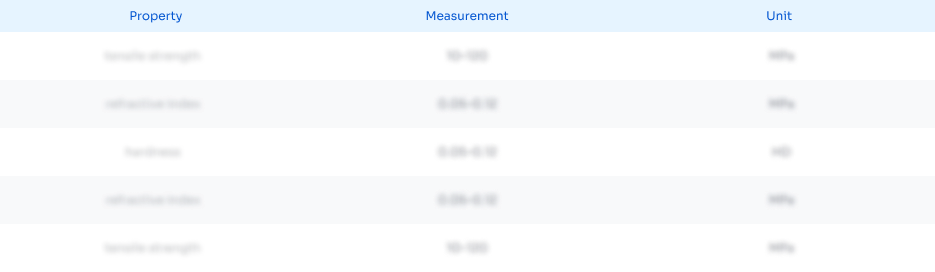
Abstract
Description
Claims
Application Information

- R&D
- Intellectual Property
- Life Sciences
- Materials
- Tech Scout
- Unparalleled Data Quality
- Higher Quality Content
- 60% Fewer Hallucinations
Browse by: Latest US Patents, China's latest patents, Technical Efficacy Thesaurus, Application Domain, Technology Topic, Popular Technical Reports.
© 2025 PatSnap. All rights reserved.Legal|Privacy policy|Modern Slavery Act Transparency Statement|Sitemap|About US| Contact US: help@patsnap.com