Warehouse logistics carrying robot
A technology for handling robots and warehousing and logistics, which is applied in the field of logistics and handling. It can solve the problems of time-consuming external disassembly of the motor wheel, reduce the safety of logistics and handling, and poor installation stability, and achieve the effects of easy replacement, improved safety, and increased stability.
- Summary
- Abstract
- Description
- Claims
- Application Information
AI Technical Summary
Problems solved by technology
Method used
Image
Examples
Embodiment
[0023] see Figure 1-5 , the present invention provides the following technical solutions: a warehousing logistics handling robot, including a drive base 1 and a tray 2, the tray 2 is installed above the drive base 1, the lower surface of the drive base 1 is provided with a wheel groove 3, and the inside of the wheel groove 3 The drive motor wheel 4 is installed, and the output shaft at both ends of the drive motor wheel 4 is integrally formed with a rotating shaft 45, and the surface of the rotating shaft 45 is provided with a limiting groove 46, and the outside of the limiting groove 46 is sleeved with a connecting clamp 6, which connects the clamping plate 6. Both ends are fixed with a leaf spring 5 by bolts, and the two ends of the leaf spring 5 are fixed on the surface of the wheel groove 3 by bolts.
[0024] In this embodiment, the rotating shaft 45 is connected to the leaf spring 5 through the connecting clamp 6, and the connecting clamp 6 is set outside the limit groov...
PUM
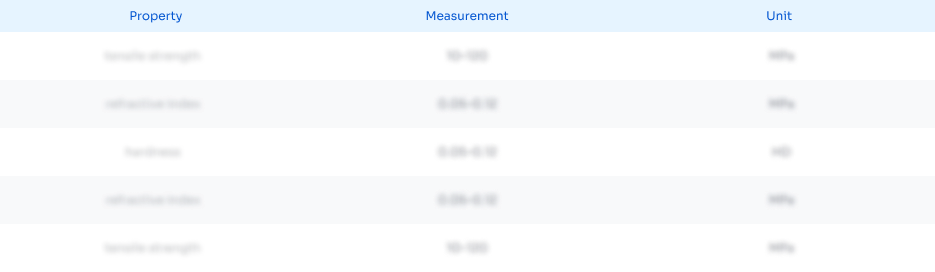
Abstract
Description
Claims
Application Information

- R&D
- Intellectual Property
- Life Sciences
- Materials
- Tech Scout
- Unparalleled Data Quality
- Higher Quality Content
- 60% Fewer Hallucinations
Browse by: Latest US Patents, China's latest patents, Technical Efficacy Thesaurus, Application Domain, Technology Topic, Popular Technical Reports.
© 2025 PatSnap. All rights reserved.Legal|Privacy policy|Modern Slavery Act Transparency Statement|Sitemap|About US| Contact US: help@patsnap.com