High-pressure diaphragm pump check valve fault diagnosis method based on vibration signal analysis
A technology of vibration signal and high-pressure diaphragm, which is applied in the field of fault diagnosis of one-way valve of high-pressure diaphragm pump, can solve the problems of reducing the correct rate of fault identification and inappropriate parameter selection, and achieves the guarantee of fault diagnosis rate, simple calculation and high reliability Effect
- Summary
- Abstract
- Description
- Claims
- Application Information
AI Technical Summary
Problems solved by technology
Method used
Image
Examples
Embodiment 1
[0041] Embodiment 1: as figure 1 As shown, a high-pressure diaphragm pump check valve fault diagnosis method based on vibration signal analysis, the specific steps of the method are as follows:
[0042] Step1. Use the acceleration sensor to measure the vibration signal of the check valve of the high-pressure diaphragm pump, collect the vibration signals of the check valve of the high-pressure diaphragm pump in normal state, stuck valve fault, and wear fault state, and obtain the vibration signal in each state;
[0043] Step2. Use the variational mode decomposition (VMD) algorithm to decompose the vibration signal data under the three states of the high-pressure diaphragm pump check valve, and determine the number of decomposed modes through the center frequency to obtain K physical meanings. Inigenmodulus function (IMF) components;
[0044] Step3. Calculate the multi-scale permutation entropy of the IMF component, and construct a high-dimensional fault feature matrix;
[004...
Embodiment 2
[0047] Embodiment 2: In this embodiment, the data of the check valve of No. 3 high-pressure diaphragm pumping station of Yunnan Dahongshan Pipeline are used for experimental analysis. Specific steps are as follows:
[0048]Step 1: Collect three different types of vibration signals of the check valve (normal, stuck valve, wear fault) at a fixed sampling frequency, the sampling frequency is f=2560, the length of the data is 3072, and 25 sets of data are collected for each state used as the total sample.
[0049] Step 2: Randomly select a group of data signals, use the VMD algorithm to decompose the vibration signal, determine the number K of the decomposed modes through the center frequency, and obtain K IMF components with physical meaning. For the number of decomposition modes K, when the number of mode decompositions is small, since the VMD algorithm is equivalent to an adaptive Wiener filter bank, some important information in the original signal will be filtered out and lo...
Embodiment 3
[0059] Embodiment 3: In order to verify the superiority of VMD decomposition for noise-containing signals, this example compares the VMD decomposition method with the local feature scale (LCD) decomposition method. During the experiment, the methods of selecting the first four decomposed components, feature extraction and fault classification are consistent with the present invention. The fault identification results of VMD and LCD decomposition methods are shown in the figure Figure 5 and Figure 6 As shown, the comparison is shown in Table 2.
[0060] It can be seen from Table 2 that when the LCD decomposition method is used, the samples in the normal state are all correctly identified, but the recognition accuracy of the stuck valve fault and wear fault containing noise is very low, and 8 stuck valve faults are misclassified as wear Faults, 3 wear faults are misclassified as normal, and the comprehensive recognition accuracy rate is only 63.33%, which is lower than 96.67...
PUM
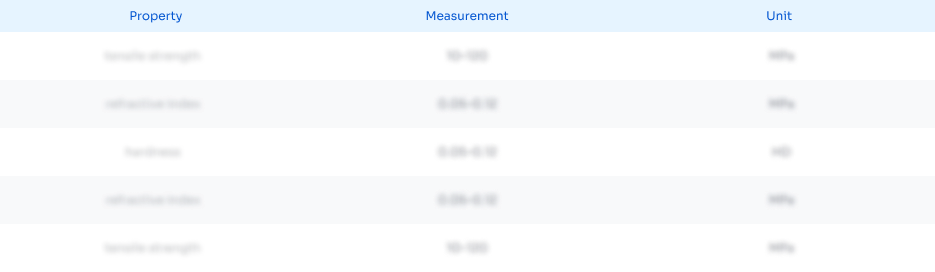
Abstract
Description
Claims
Application Information

- R&D
- Intellectual Property
- Life Sciences
- Materials
- Tech Scout
- Unparalleled Data Quality
- Higher Quality Content
- 60% Fewer Hallucinations
Browse by: Latest US Patents, China's latest patents, Technical Efficacy Thesaurus, Application Domain, Technology Topic, Popular Technical Reports.
© 2025 PatSnap. All rights reserved.Legal|Privacy policy|Modern Slavery Act Transparency Statement|Sitemap|About US| Contact US: help@patsnap.com