SCR inlet flue gas pre-treatment system and method
A flue gas and inlet technology is applied in the field of pollutant control of layer-fired coal-fired boilers to achieve the effects of reducing escape, improving economy and simple system
- Summary
- Abstract
- Description
- Claims
- Application Information
AI Technical Summary
Problems solved by technology
Method used
Image
Examples
specific Embodiment approach 1
[0052] Specific implementation mode one: as figure 1 and 2 As shown, the SCR inlet flue gas pretreatment system and method of direct pyrolysis in a urea flue described in this embodiment:
[0053] The bed-fired coal-fired boiler equipped with the SCR flue gas denitrification system includes the bed-fired coal-fired boiler furnace 4, the burnout chamber 21, the convection tube bundle 5, the flue, the SCR inlet flue gas pretreatment system, the SCR device 17, and the economizer 18 , air preheater 19, etc.; the flue gas produced at the grate 2 of the layer-fired coal-fired boiler passes through the hearth 4 of the layer-fired coal-fired boiler, the burnout chamber 21, and sprays urea solution into the burnout chamber, and the high-temperature flue gas Under the action, pyrolysis forms NH3 mixed into the flue gas, and then the flue gas flows through the convection tube bundle 5, enters the flue gas pretreatment system at the SCR inlet, performs uniform temperature adjustment and...
specific Embodiment approach 2
[0061] Specific implementation mode two: it differs from specific implementation scheme one in that: if image 3 , the cooling method of the temperature adjustment system of the flue gas pretreatment system at the SCR inlet, the cooling method is canceled by drawing low-temperature flue gas from the flue gas at the outlet of the boiler dust collector or the flue gas at the outlet of the air preheater to cool down; by adding a thermostat economizer Cool down.
[0062] The temperature regulation system of the flue gas pretreatment system at the SCR inlet, the cooling method is that the flue gas flowing out from the convection tube bundle 5 of the boiler is cooled by the temperature regulation economizer 13 . The cooling water on the working medium side of the temperature-adjusting economizer comes from the boiler feed water at the inlet of the boiler economizer 18, and the water heated up by the temperature-adjusting economizer 13 returns to the inlet of the boiler economizer 18...
specific Embodiment approach 3
[0063] Specific implementation mode three: the difference with specific implementation mode two is: if Figure 4 , in the transformation of old boilers, a smoke barrier 20 can be installed at the outlet of the boiler tube bundle 5, and the flue gas passes through the temperature adjustment system, the cyclone separator 12, the equalizer plate 16 and the SCR reaction device 17 from above the smoke barrier, Return to the bottom of the smoke baffle 20, and enter the original economizer 18 and air preheater 19 of the boiler, and then exit the boiler.
[0064] Other components and connections are the same as those in the second embodiment.
PUM
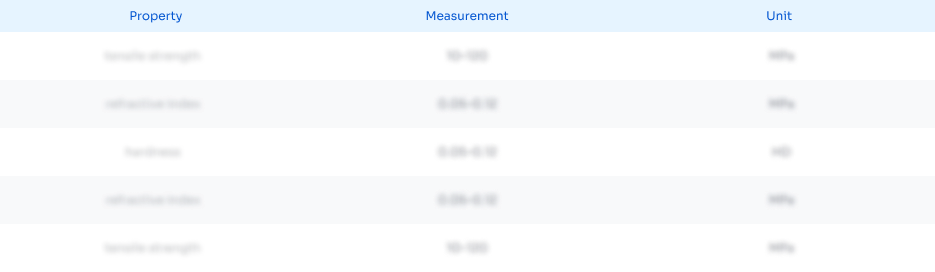
Abstract
Description
Claims
Application Information

- Generate Ideas
- Intellectual Property
- Life Sciences
- Materials
- Tech Scout
- Unparalleled Data Quality
- Higher Quality Content
- 60% Fewer Hallucinations
Browse by: Latest US Patents, China's latest patents, Technical Efficacy Thesaurus, Application Domain, Technology Topic, Popular Technical Reports.
© 2025 PatSnap. All rights reserved.Legal|Privacy policy|Modern Slavery Act Transparency Statement|Sitemap|About US| Contact US: help@patsnap.com