Finite element simulation modeling method suitable for longitudinal torsion ultrasonic milling
A simulation modeling and finite element technology, applied in design optimization/simulation, special data processing applications, instruments, etc., can solve the problems of long calculation time, complex model, inability to accurately reflect cutting force, etc., to achieve good economic benefits, easy to use. The effect of promotion
- Summary
- Abstract
- Description
- Claims
- Application Information
AI Technical Summary
Problems solved by technology
Method used
Image
Examples
Embodiment
[0044] Example: see Figure 1-Figure 6 . A finite element simulation modeling method suitable for longitudinal torsion ultrasonic milling. Set the following parameters: milling cutter rake angle 5°, relief angle 12°, helix angle 30°, cutting edge radius 0.01mm, cutting speed 25m / min, per tooth Feed rate 0.008mm / z, radial depth of cut 0.15mm, axial depth of cut 2mm, longitudinal vibration amplitude 5μm, torsion amplitude 4μm, longitudinal torsion frequency 35kHz, longitudinal torsion phase difference 90°, tool material parameters are shown in Table 1. , The workpiece material parameters are shown in Tables 2 and 3, and the workpiece material unit failure criterion parameters are shown in Table 4.
[0045] Table 1 Tool material parameters
[0046]
[0047] Table 2 Workpiece material parameters
[0048]
[0049] Table 3 Constitutive parameters of workpiece material
[0050]
[0051] Table 4 Parameters of unit failure criterion of workpiece material
[0052]
[0053] According to the de...
PUM
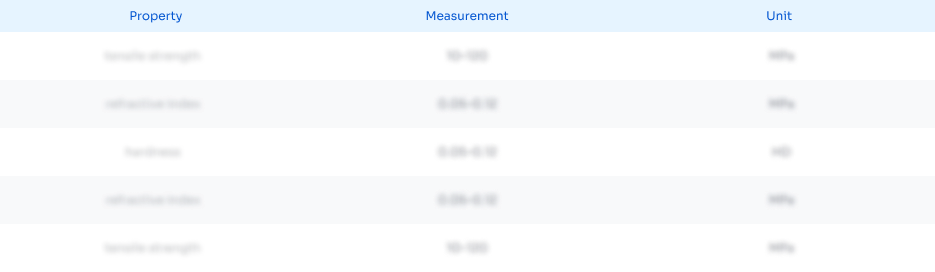
Abstract
Description
Claims
Application Information

- R&D
- Intellectual Property
- Life Sciences
- Materials
- Tech Scout
- Unparalleled Data Quality
- Higher Quality Content
- 60% Fewer Hallucinations
Browse by: Latest US Patents, China's latest patents, Technical Efficacy Thesaurus, Application Domain, Technology Topic, Popular Technical Reports.
© 2025 PatSnap. All rights reserved.Legal|Privacy policy|Modern Slavery Act Transparency Statement|Sitemap|About US| Contact US: help@patsnap.com