An ultra-high voltage forming foil forming process for aluminum electrolytic capacitors
An aluminum electrolytic capacitor and ultra-high voltage technology, applied in the direction of electrolytic capacitors, capacitors, electrolytic coatings, etc., can solve the problems of low reaching voltage, poor life, flash fire, etc. The effect of reducing the concentration of negative ions
- Summary
- Abstract
- Description
- Claims
- Application Information
AI Technical Summary
Problems solved by technology
Method used
Image
Examples
Embodiment 1
[0029] Step 1: Take the 99.99% aluminum foil after electrolytic corrosion treatment and immerse it in pure water at 97°C for 15 minutes;
[0030] The second step: in the first stage, the concentration of boric acid is 50g / L, the concentration of citric acid is 5g / L, the concentration of ammonium pentaborate is 10g / L, the temperature of the bath is 85°C, the formation voltage is 220V, and the current density is 50mA / cm 2 , the formation time is 8 minutes;
[0031] The third step: in the second stage, the concentration of boric acid is 50g / L, the concentration of citric acid is 1g / L, the concentration of ammonium pentaborate is 6g / L, the temperature of the bath is 85°C, the formation voltage is 450V, and the current density is 35mA / cm 2 , the formation time is 8 minutes;
[0032] The fourth step: in the third stage, the concentration of boric acid is 50g / L, the concentration of tetramethylammonium hydroxide is 0.35g / L, the concentration of mannitol is 1g / L, the temperature of t...
Embodiment 2
[0042] Example 2 except the eighth step: immerse the fourth grade of the foil that has been chemically converted for the second time in an aqueous phosphoric acid solution with a concentration of 50ml / L at 60°C for 6 minutes; there are some differences from Example 1, and the rest of the steps are the same as Example 1 .
Embodiment 3
[0056] Step 1: Take the 99.99% aluminum foil after electrolytic corrosion treatment and soak it in pure water at 97°C for 16 minutes;
[0057] The second step: in the first stage, the concentration of boric acid is 50g / L, the concentration of citric acid is 2g / L, the concentration of ammonium pentaborate is 10g / L, the temperature of the bath is 85°C, the formation voltage is 260V, and the current density is 50mA / cm 2 , the formation time is 8 minutes;
[0058] The third step: in the second stage, the concentration of boric acid is 50g / L, the concentration of citric acid is 0.5g / L, the concentration of ammonium pentaborate is 1g / L, the temperature of the bath is 85°C, the formation voltage is 530V, and the current density is 35mA / cm 2 , the formation time is 8 minutes;
[0059] The fourth step: use boric acid concentration of 50g / L in the third stage, tetramethylammonium hydroxide concentration of 0.25g / L, mannitol concentration of 0.5g / L, bath temperature of 85°C, formation v...
PUM
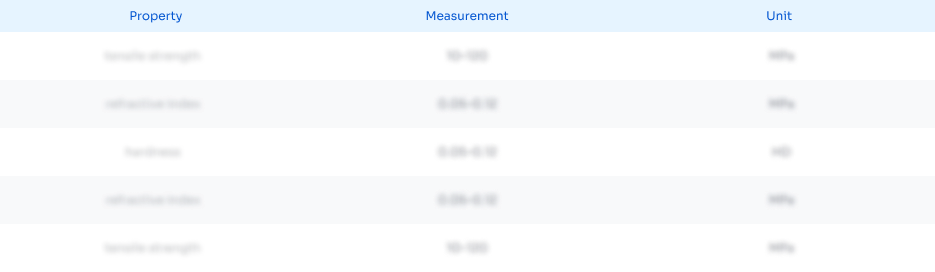
Abstract
Description
Claims
Application Information

- R&D Engineer
- R&D Manager
- IP Professional
- Industry Leading Data Capabilities
- Powerful AI technology
- Patent DNA Extraction
Browse by: Latest US Patents, China's latest patents, Technical Efficacy Thesaurus, Application Domain, Technology Topic, Popular Technical Reports.
© 2024 PatSnap. All rights reserved.Legal|Privacy policy|Modern Slavery Act Transparency Statement|Sitemap|About US| Contact US: help@patsnap.com