Method for surface modification of carbon fibers by sizing agent containing carbon nanomaterials
A technology of surface modification and nanomaterials, applied in the direction of carbon fiber, fiber type, fiber treatment, etc., can solve the problems of poor fracture toughness, low interface strength, etc., and achieve the effect of improved mechanical properties, increased tensile strength, and good continuity
- Summary
- Abstract
- Description
- Claims
- Application Information
AI Technical Summary
Problems solved by technology
Method used
Image
Examples
Embodiment 1
[0018] Take 12 sections of T300B carbon fiber (15 cm each), soak them in acetone for 2 h, rinse them with deionized water, dry them in vacuum, and take them out for later use. Control the mass fraction of epoxy resin E-51 in DMF to be 0.5%, add E-51 to DMF, stir with a magnetic stirrer until E51 is completely dissolved, then add weighed GnP, CNTs and TETA, and finally The beaker was placed in an ultrasonic cell pulverizer for ultrasonication for 2 h to prepare a GnP-CNTs sizing agent with a mass fraction of 0.4%. The mass ratio of GnP and CNTs in the sizing agent was 1:4, and the mass ratio of E51 and TETA was 20:1. Pour the GnP-CNTs sizing agent into the aluminum box, then put the spare CF in the GnP-CNTs sizing agent and completely immerse it, take it out after 10 s and scrape off the residual liquid droplets on the fiber, and finally fix the CF on both sides of the aluminum box. The ends were dried in a vacuum oven at 60°C for 1 h, and the modified CF was obtained.
Embodiment 2
[0020] Take 12 sections of T300B carbon fiber (15 cm each), soak them in acetone for 2 h, rinse them with deionized water, dry them in vacuum, and take them out for later use. Control the mass fraction of epoxy resin E-51 in DMF to be 0.5%, add E-51 to DMF, stir with a magnetic stirrer until E51 is completely dissolved, then add weighed GnP, CNTs and TETA, and finally The beaker was placed in an ultrasonic cell pulverizer for 2 hours of sonication, and a GnP-CNTs sizing agent with a mass fraction of 0.4% was prepared. The mass ratio of GnP and CNTs in the sizing agent is 1:4, and the mass ratio of E51 and TETA is 20:1; pour the prepared GnP-CNTs sizing agent into the aluminum box, and then put the spare CF in the GnP-CNTs Completely submerged in the sizing agent, took it out after 20 s and scraped off the residual liquid droplets on the fiber, and finally fixed the CF on both ends of the aluminum box and dried it in a vacuum drying oven at 60°C for 1 h to obtain the modified C...
Embodiment 3
[0022] Take 12 sections of T300B carbon fiber (15 cm each), soak them in acetone for 2 h, rinse them with deionized water, dry them in vacuum, and take them out for later use. Control the mass fraction of epoxy resin E-51 in DMF to be 0.5%, add E-51 to DMF, stir with a magnetic stirrer until E51 is completely dissolved, then add weighed GnP, CNTs and TETA, and finally The beaker was placed in an ultrasonic cell pulverizer for ultrasonication for 2 h to prepare a GnP-CNTs sizing agent with a mass fraction of 0.4%. The mass ratio of GnP and CNTs in the sizing agent was 1:4, and the mass ratio of E51 and TETA was 20:1. Pour the GnP-CNTs sizing agent into the aluminum box, then put the spare CF in the GnP-CNTs sizing agent and completely submerge it, take it out after 30 s and scrape off the residual liquid droplets on the fiber, and finally fix the CF on both sides of the aluminum box. The ends were dried in a vacuum oven at 60°C for 1 h, and the modified CF was obtained.
PUM
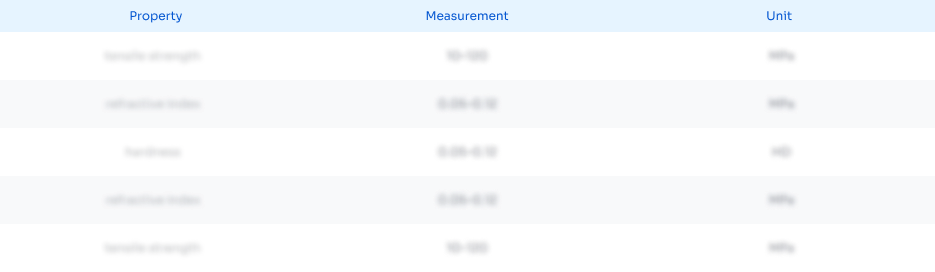
Abstract
Description
Claims
Application Information

- R&D
- Intellectual Property
- Life Sciences
- Materials
- Tech Scout
- Unparalleled Data Quality
- Higher Quality Content
- 60% Fewer Hallucinations
Browse by: Latest US Patents, China's latest patents, Technical Efficacy Thesaurus, Application Domain, Technology Topic, Popular Technical Reports.
© 2025 PatSnap. All rights reserved.Legal|Privacy policy|Modern Slavery Act Transparency Statement|Sitemap|About US| Contact US: help@patsnap.com