Extra high voltage composite insulator polyurethane glass fiber core rod, and preparation method thereof
A polyurethane glass fiber core rod and polyurethane glass fiber core technology are applied in the field of composite core rods for composite insulators, which can solve radial bending, torsion, shearing, poor impact strength, limit the application field of composite insulators, and produce tensile strings. Low efficiency and other problems, to achieve the effect of ensuring strength, good surface finish and high production efficiency
- Summary
- Abstract
- Description
- Claims
- Application Information
AI Technical Summary
Problems solved by technology
Method used
Examples
Embodiment
[0016] Preparation of the present invention comprises the steps:
[0017] Step 1: Pretreat the continuous glass fiber roving with a coupling agent, and treat it with an ultrasonic device during the treatment process to ensure uniform infiltration and dispersion to achieve a good surface treatment effect;
[0018] Step 2: Send the continuous glass fiber roving processed in step 1 into the preforming mold, and feed it into the polyurethane resin through the injection pump, so that the glass fiber is fully impregnated with it, so that the polyurethane resin structure is formed around the continuous glass fiber roving ;
[0019] Step 3: The continuous glass fiber roving is subjected to a pultrusion process to finally obtain the composite mandrel.
[0020] During processing, strict requirements are defined for the environment. In the process of glass fiber surface modification and impregnation, ultrasonic technology is applied to ensure that the material mixing and impregnation a...
PUM
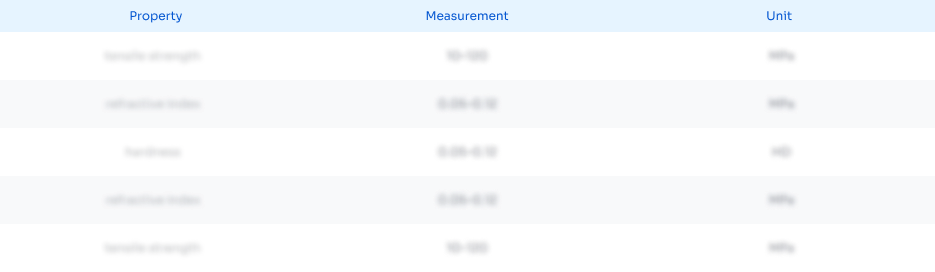
Abstract
Description
Claims
Application Information

- R&D Engineer
- R&D Manager
- IP Professional
- Industry Leading Data Capabilities
- Powerful AI technology
- Patent DNA Extraction
Browse by: Latest US Patents, China's latest patents, Technical Efficacy Thesaurus, Application Domain, Technology Topic, Popular Technical Reports.
© 2024 PatSnap. All rights reserved.Legal|Privacy policy|Modern Slavery Act Transparency Statement|Sitemap|About US| Contact US: help@patsnap.com