Rotational moulding preparation process of air mover shell
A preparation process and shell technology, which is applied in the field of rotational molding preparation process of the shell of a floor blower, can solve problems such as burrs easily generated in products, and achieve the effects of reducing the probability of burrs, improving insect resistance and improving economic efficiency.
- Summary
- Abstract
- Description
- Claims
- Application Information
AI Technical Summary
Problems solved by technology
Method used
Image
Examples
Embodiment Construction
[0036] The following is attached figure 1 The present invention is described in further detail.
[0037] A rotational molding preparation process for a floor blower shell, comprising the following steps:
[0038] Step 1: Adjust the speed of the mill to 5000r / min, add 55 kg of raw material particles per bag into the mill for grinding, each bag requires 25 minutes of milling time, and finally get the raw material powder;
[0039] Step 2: Add 100 g of toner to the raw material powder obtained in Step 1, then add 7 kg of waste materials of the same color, and then pour all of them into a blender and stir for 30 minutes to obtain a mixed powder;
[0040] Step 3: Evenly spray the release agent on the inside of the lower mold of the mold, weigh the mixed powder with the required weight with an electronic scale, and pour it into the lower mold of the mold;
[0041] Step 4: After the molds are combined, install the molds on the tray of the rotary frame, connect the upper mold and the...
PUM
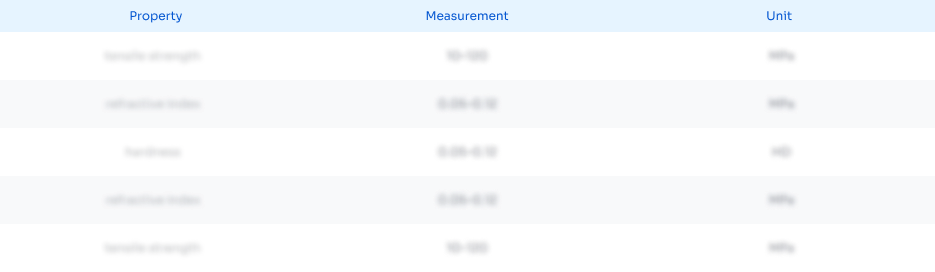
Abstract
Description
Claims
Application Information

- R&D
- Intellectual Property
- Life Sciences
- Materials
- Tech Scout
- Unparalleled Data Quality
- Higher Quality Content
- 60% Fewer Hallucinations
Browse by: Latest US Patents, China's latest patents, Technical Efficacy Thesaurus, Application Domain, Technology Topic, Popular Technical Reports.
© 2025 PatSnap. All rights reserved.Legal|Privacy policy|Modern Slavery Act Transparency Statement|Sitemap|About US| Contact US: help@patsnap.com