Corner stamping and blanking rough die for metal cutting part top block frame air defence stress marks
A metal cutting and stress trace technology, applied in metal processing equipment, forming tools, manufacturing tools, etc., can solve the problems of limit deviation, surface texture reflection, upper or lower initial position of fitting, etc.
- Summary
- Abstract
- Description
- Claims
- Application Information
AI Technical Summary
Problems solved by technology
Method used
Image
Examples
Embodiment Construction
[0032]In order to make the technical means, creative features, goals and effects achieved by the present invention easy to understand, the present invention will be further described below in conjunction with specific embodiments.
[0033] see Figure 1-Figure 9 , the present invention provides a corner stamping and roughening mold for preventing stress marks on the top block of metal cutting parts. Groove 5, thimble groove 6, base 7, the base 7 is buckled together with the top cover plate 3 through the clamping column 4, and the top cover plate 3 and the base 7 are respectively installed in the parting stamping groove 5 The upper and lower sides of the upper and lower sides are parallel to each other, the parting stamping groove 5 and the thimble groove 6 are nested into one body, and the air pipe insertion hole 1 and the rubber ring 2 are respectively provided with more than two and are both nested in the top cover plate 3 inside and on the same horizontal plane, the clampi...
PUM
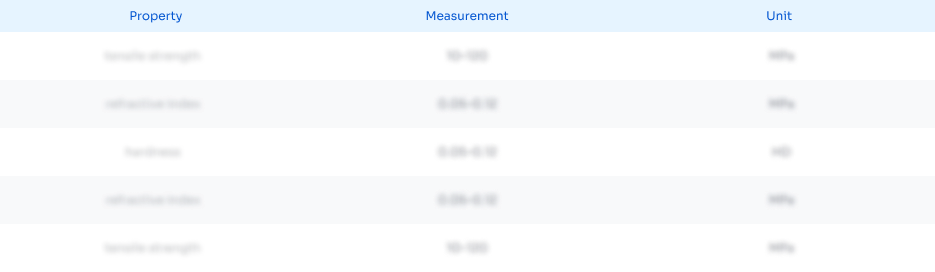
Abstract
Description
Claims
Application Information

- R&D
- Intellectual Property
- Life Sciences
- Materials
- Tech Scout
- Unparalleled Data Quality
- Higher Quality Content
- 60% Fewer Hallucinations
Browse by: Latest US Patents, China's latest patents, Technical Efficacy Thesaurus, Application Domain, Technology Topic, Popular Technical Reports.
© 2025 PatSnap. All rights reserved.Legal|Privacy policy|Modern Slavery Act Transparency Statement|Sitemap|About US| Contact US: help@patsnap.com