A preparation method based on carbonized melamine foam@Bi2O3 nanosheet supercapacitor electrode material
A carbonized melamine and supercapacitor technology, which is applied in hybrid capacitor electrodes, carbon preparation/purification, chemical instruments and methods, etc., can solve the problems of low redox reversibility, poor cycle stability, low capacitance, etc., and shorten the diffusion path , good electrical conductivity, high specific surface area
- Summary
- Abstract
- Description
- Claims
- Application Information
AI Technical Summary
Problems solved by technology
Method used
Image
Examples
Embodiment 1
[0028] (1) The melamine foam sample (13.0×2.5×2.5 cm 3 ) on a quartz boat and placed in a tube furnace. Before pyrolysis, the sample was passed through argon gas at room temperature for 10-30 min, and the flow rate of argon gas was 1000 standard cubic centimeters per minute, and the air inside was exhausted. The melamine foam was pyrolyzed at 600-800 °C for 1-2 h, and the heating rate was 5-10 °C / min to reach the highest temperature. After pyrolysis, the sample temperature slowly returned to room temperature. The entire heating and cooling process is carried out under continuous argon at 500-1000 sccm / min.
[0029] (2) Weigh 0.97 g of bismuth nitrate pentahydrate and dissolve it in the mixture of ethanol and ethylene glycol, stir and dissolve to obtain a dispersion.
[0030] (3) Cut a small piece of the carbonized melamine foam obtained in step (1) into a polytetrafluoroethylene hydrothermal reaction kettle, and pour the uniform dispersion obtained in step (2) into it for hy...
Embodiment 2
[0034] (1) The melamine foam sample (13.0×2.5×2.5 cm 3) on a quartz boat and placed in a tube furnace. Before pyrolysis, the sample was passed through argon gas at room temperature for 10-30 min, and the flow rate of argon gas was 1000 standard cubic centimeters per minute, and the air inside was exhausted. The melamine foam was pyrolyzed at 600-800 °C for 1-2 h, and the heating rate was 5-10 °C / min to reach the highest temperature. After pyrolysis, the sample temperature rose slowly to 25-40 °C. The entire heating and cooling process is carried out under continuous argon at 500-1000 sccm / min.
[0035] (2) Weigh 1.455 g bismuth nitrate pentahydrate and dissolve it in the mixture of ethanol and ethylene glycol, stir and dissolve to obtain a dispersion.
[0036] (3) Cut a small piece of the carbonized melamine foam obtained in step (1) into a polytetrafluoroethylene hydrothermal reaction kettle, and pour the uniform dispersion obtained in step (2) into it for hydrothermal reac...
Embodiment 3
[0040] (1) The melamine foam sample (13.0×2.5×2.5 cm 3 ) on a quartz boat and placed in a tube furnace. Before pyrolysis, the sample was passed through argon gas at room temperature for 10-30 min, and the flow rate of argon gas was 1000 standard cubic centimeters per minute, and the air inside was exhausted. The melamine foam was pyrolyzed at 600-800 °C for 1-2 h, and the heating rate was 5-10 °C / min to reach the highest temperature. After pyrolysis, the sample temperature rose slowly to 25-40 °C. The entire heating and cooling process is carried out under continuous argon at 500-1000 sccm / min.
[0041] (2) Weigh 1.94 g of bismuth nitrate pentahydrate and dissolve it in the mixture of ethanol and ethylene glycol, stir and dissolve to obtain a dispersion.
[0042] (3) Cut a small piece of the carbonized melamine foam obtained in step (1) into a polytetrafluoroethylene hydrothermal reaction kettle, and pour the uniform dispersion obtained in step (2) into it for hydrothermal r...
PUM
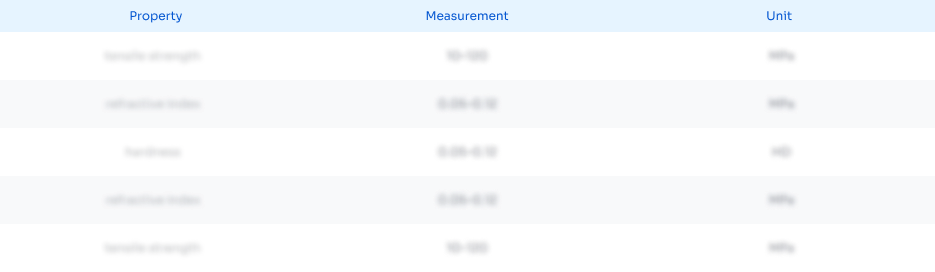
Abstract
Description
Claims
Application Information

- R&D Engineer
- R&D Manager
- IP Professional
- Industry Leading Data Capabilities
- Powerful AI technology
- Patent DNA Extraction
Browse by: Latest US Patents, China's latest patents, Technical Efficacy Thesaurus, Application Domain, Technology Topic, Popular Technical Reports.
© 2024 PatSnap. All rights reserved.Legal|Privacy policy|Modern Slavery Act Transparency Statement|Sitemap|About US| Contact US: help@patsnap.com