T-shaped node of steel concrete combined pipe assembled by long channel steel and threaded sleeve
A technology of threaded casing and combined pipe, applied in building types, protective buildings/shelters, building components, etc., can solve problems such as deformation of prefabricated walls, poor seismic resistance, cracks, etc., to ensure construction quality, improve High connection strength and high construction efficiency
- Summary
- Abstract
- Description
- Claims
- Application Information
AI Technical Summary
Problems solved by technology
Method used
Image
Examples
Embodiment Construction
[0014] Such as figure 1 As shown, the long-shaped steel and threaded casing combined steel-concrete composite pipe T-shaped node of the present invention includes a first steel-concrete composite pipe and a second steel-concrete composite pipe arranged perpendicular to each other, and the first steel-concrete composite pipe The rear side is adjacent to the front end of the second steel-concrete composite pipe. The first steel-concrete composite pipe includes a first rectangular steel plate structure 1 and a first concrete layer 2 poured on the outer side of the first rectangular steel plate structure 1, and a second steel-concrete composite pipe Including a second rectangular steel plate structure 3 and a second concrete layer 4 poured on the outer side of the second rectangular steel plate structure 3. A number of first screw rods are inserted between the front side plate and the rear side plate of the first rectangular steel plate structure 1 The ribs 5, the front and rear en...
PUM
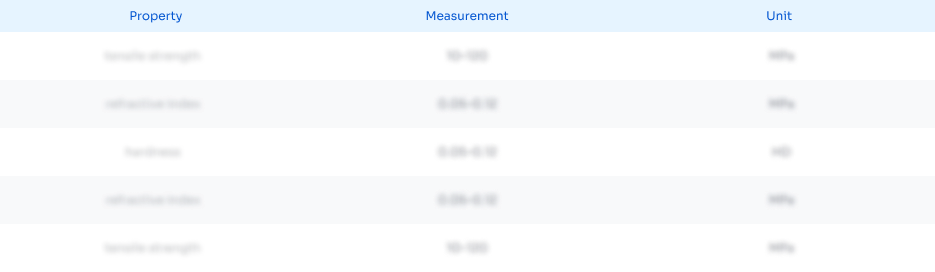
Abstract
Description
Claims
Application Information

- R&D
- Intellectual Property
- Life Sciences
- Materials
- Tech Scout
- Unparalleled Data Quality
- Higher Quality Content
- 60% Fewer Hallucinations
Browse by: Latest US Patents, China's latest patents, Technical Efficacy Thesaurus, Application Domain, Technology Topic, Popular Technical Reports.
© 2025 PatSnap. All rights reserved.Legal|Privacy policy|Modern Slavery Act Transparency Statement|Sitemap|About US| Contact US: help@patsnap.com