Gaseous phase etherifying production method of complex ether with mixed phenol methanol
A mixed phenol and etherification technology, applied in the field of catalysis, can solve problems such as poor economy and high hydrogen consumption
- Summary
- Abstract
- Description
- Claims
- Application Information
AI Technical Summary
Problems solved by technology
Method used
Image
Examples
Embodiment 1
[0127] The preparation process of the catalyst is as follows: 120 grams of ZSM-5 molecular sieve with a molar silicon-aluminum ratio of 20 is mixed with 60 grams of diatomaceous earth and 100 grams of silica sol containing 20% by weight of silicon dioxide, and an appropriate amount of 10% dilute Nitric acid is used as extrusion aid to extrude strips. Dry at 120°C and bake at 500°C for 10 hours. The above catalyst is cut into 1-3mm to prepare columnar catalyst precursor A0. A1 was obtained by steaming 20 grams of A0 in a 100% steam atmosphere for 10 hours at a temperature of 350°C and calcining at 550°C for 3 hours. Add 50ml weight content, 5% phosphoric acid aqueous solution to 20 grams of A1, soak at 30 ℃ for 4 hours. Drying at 120°C and calcining at 550°C for 10 hours prepared Catalyst A, wherein the molecular sieve content was 60%.
Embodiment 2
[0129] The preparation process of the catalyst is as follows: 170 grams of ZSM-5 molecular sieve with a molar silicon-aluminum ratio of 30 is mixed with 30 grams of alumina, and an appropriate amount of 10% dilute nitric acid is added as an extrusion aid to extrude. Dry at 120°C and bake at 700°C for 4 hours. Above-mentioned catalyst is cut into 1~3mm and makes columnar catalyst parent body B0. The parent body catalyst B0 of 20 grams carries out steam treatment in 100% steam atmosphere for 1 hour, and treatment temperature is 700 ℃, and 550 ℃ roasts 3 hours and makes B1, will Add 50ml of 3% by weight phosphoric acid solution to 20 grams of B1 and soak at room temperature for 10 hours. Dry at 120°C and calcinate at 600°C for 2 hours to prepare Catalyst B. The molecular sieve content in the catalyst is 85%.
Embodiment 3
[0131] The preparation process of the catalyst is as follows: 200 grams of ZSM-5 molecular sieve with a molar silicon-aluminum ratio of 40 is mixed with 20 grams of diatomaceous earth, 100 grams of silicon dioxide and 30% silica sol by weight, and an appropriate amount of 10% dilute nitric acid is added as an extrusion aid Extrusion molding. Dry at 120°C and bake at 550°C for 4 hours. The above-mentioned catalyst was cut into 1-3 mm to obtain columnar catalyst matrix D0. The matrix catalyst D0 sample of 20 grams was impregnated with barium nitrate solution aqueous solution for 24 hours, dried at 120°C, and roasted at 600°C for 3 hours. The weight percentage of barium oxide in the catalyst was 0.1% To prepare D1, 20 grams of D1 was steam treated for 10 hours in a 100% steam atmosphere, the treatment temperature was 350°C, and roasted at 550°C for 3 hours to obtain D2, 20 grams of D2 was added to 50ml, with a weight content of 10% Nitric acid solution, soak at room temperature ...
PUM
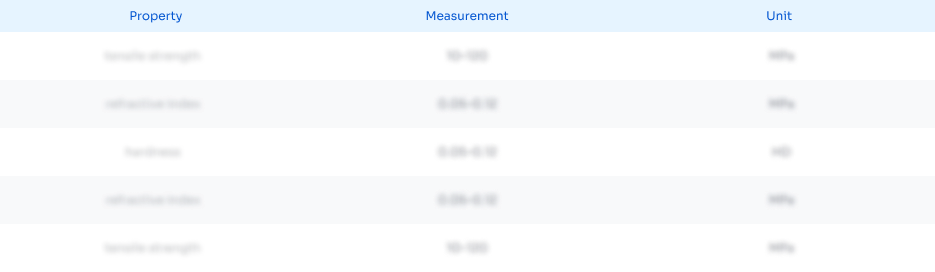
Abstract
Description
Claims
Application Information

- R&D
- Intellectual Property
- Life Sciences
- Materials
- Tech Scout
- Unparalleled Data Quality
- Higher Quality Content
- 60% Fewer Hallucinations
Browse by: Latest US Patents, China's latest patents, Technical Efficacy Thesaurus, Application Domain, Technology Topic, Popular Technical Reports.
© 2025 PatSnap. All rights reserved.Legal|Privacy policy|Modern Slavery Act Transparency Statement|Sitemap|About US| Contact US: help@patsnap.com