Method for carrying out hot stamping on printed product
A technology for printed products and hot stamping plates, which is applied in the field of hot stamping for printed products. It can solve the problems of cumbersome plate alignment operations, low work efficiency, and long time consumption, and achieves saving plate loading time, uniform pressure, and uniform heating Effect
- Summary
- Abstract
- Description
- Claims
- Application Information
AI Technical Summary
Problems solved by technology
Method used
Examples
Embodiment 1
[0021] A method for hot stamping printed matter, the steps are:
[0022] (1) 30 parts of hyperbranched urethane acrylate (made by the method described in the following literature, the same below: Qian Ting, Xie Hui, Huang Li, Jin Aihong. Synthesis of hyperbranched urethane acrylate and its cured film properties [J] .Thermosetting resin, 2012,27(05):31-35.), 20 parts of modified epoxy acrylate (B5293), 8 parts of trimethylolpropane triacrylate (Changxing EM231), 0.3 parts of defoamer DF258 , 0.5 parts of wetting agent BYK P104S, 0.3 parts of leveling agent RF339 are mixed, ultrasonically dispersed at room temperature for 40 minutes, then 3 parts of photoinitiator 1173 are added, and stirred evenly to obtain UV primer;
[0023] (2) Lay the printing material (printed on coated paper) on the printing table, print UV primer on the surface of the printing material, UV light makes the varnish solidify on the surface of the printing material, and the curing time is 6s;
[0024] (3) S...
Embodiment 2
[0028] A method for hot stamping printed matter, the steps are:
[0029] (1) Wet 30 parts of hyperbranched polyurethane acrylate, 20 parts of modified epoxy acrylate (B5293), 8 parts of trimethylolpropane triacrylate (Changxing EM231), 0.3 part of defoamer DF258, and 0.5 part of wetting After mixing agent BYK P104S and 0.3 parts of leveling agent RF339, ultrasonically disperse at room temperature for 40 minutes, then add 3 parts of photoinitiator 1173, and stir evenly to obtain UV primer;
[0030] (2) Lay the printing material (printed on coated paper) on the printing table, print UV primer on the surface of the printing material, UV light makes the varnish solidify on the surface of the printing material, and the curing time is 6s;
[0031] (3) Select the hot stamping plate according to the pattern to be hot stamped, wherein the upper surface of the hot stamping plate is flat, the lower surface is the hot stamping surface, and the hot stamping surface of the hot stamping plat...
Embodiment 3
[0035] A method for hot stamping printed matter, the steps are:
[0036] (1) Wet 30 parts of hyperbranched polyurethane acrylate, 20 parts of modified epoxy acrylate (B5293), 8 parts of trimethylolpropane triacrylate (Changxing EM231), 0.3 part of defoamer DF258, and 0.5 part of wetting After mixing agent BYK P104S and 0.3 parts of leveling agent RF339, ultrasonically disperse at room temperature for 40 minutes, then add 3 parts of photoinitiator 1173, and stir evenly to obtain UV primer;
[0037] (2) Lay the printing material (printed on coated paper) on the printing table, print UV primer on the surface of the printing material, UV light makes the varnish solidify on the surface of the printing material, and the curing time is 6s;
[0038] (3) Select the hot stamping plate according to the pattern to be hot stamped, wherein the upper surface of the hot stamping plate is flat, the lower surface is the hot stamping surface, and the hot stamping surface of the hot stamping plat...
PUM
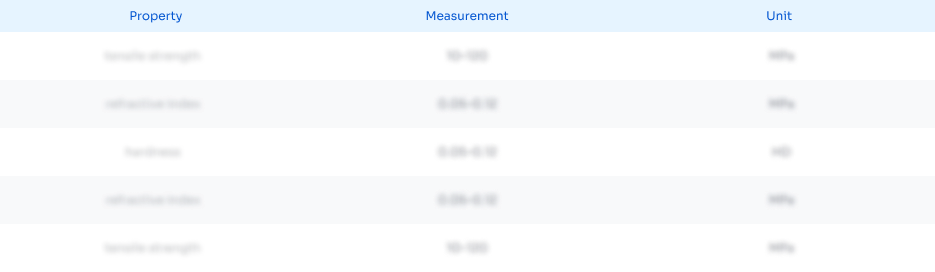
Abstract
Description
Claims
Application Information

- R&D
- Intellectual Property
- Life Sciences
- Materials
- Tech Scout
- Unparalleled Data Quality
- Higher Quality Content
- 60% Fewer Hallucinations
Browse by: Latest US Patents, China's latest patents, Technical Efficacy Thesaurus, Application Domain, Technology Topic, Popular Technical Reports.
© 2025 PatSnap. All rights reserved.Legal|Privacy policy|Modern Slavery Act Transparency Statement|Sitemap|About US| Contact US: help@patsnap.com