A flexible resistance welding device for thermoplastic composite materials
A composite material and resistance welding technology, which is applied in the direction of household appliances, other household appliances, household components, etc., can solve problems such as uneven current density, overheating of composite materials, and difficulty in handling welding work, so as to ensure welding quality and stability , Ensure the accuracy of the installation position, improve the effect of welding stability
- Summary
- Abstract
- Description
- Claims
- Application Information
AI Technical Summary
Problems solved by technology
Method used
Image
Examples
Embodiment Construction
[0025] The structure of the present invention will be further described below in conjunction with the accompanying drawings and through embodiments. It should be noted that this embodiment is illustrative rather than limiting.
[0026] like Figure 1 to Figure 5 As shown, the thermoplastic composite flexible resistance welding device provided by the present invention includes a servo drive motor 1, a precision ball guide linear motion system 2 and a thermoplastic composite resistance welding platform 3; wherein the precision ball guide linear motion system 2 is a cuboid structure, and the top A track is provided along the length direction, and the power output is provided by the servo drive motor 1; the thermoplastic composite material resistance welding platform 3 is installed on the precision ball guide linear motion system 2 in a manner that can move along the upper track of the precision ball guide linear motion system 2.
[0027] The thermoplastic composite material resi...
PUM
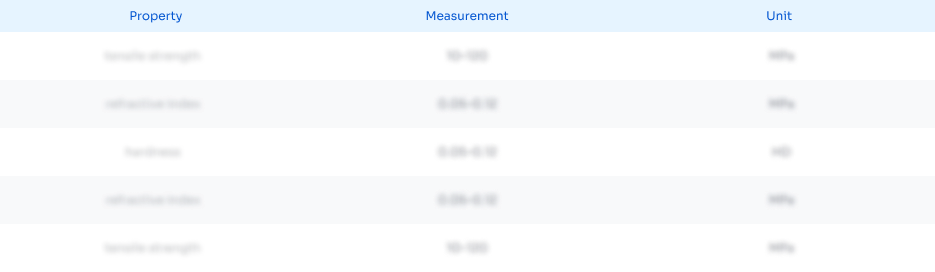
Abstract
Description
Claims
Application Information

- R&D
- Intellectual Property
- Life Sciences
- Materials
- Tech Scout
- Unparalleled Data Quality
- Higher Quality Content
- 60% Fewer Hallucinations
Browse by: Latest US Patents, China's latest patents, Technical Efficacy Thesaurus, Application Domain, Technology Topic, Popular Technical Reports.
© 2025 PatSnap. All rights reserved.Legal|Privacy policy|Modern Slavery Act Transparency Statement|Sitemap|About US| Contact US: help@patsnap.com