Neutron-shielding aluminum-based composite material and preparation method thereof
A technology of aluminum matrix composite material and matrix material, applied in the field of neutron shielding aluminum matrix composite material and its preparation, can solve the problems of poor comprehensive performance of materials and single shielding effect, and achieve the effects of good heat resistance and good application reliability
- Summary
- Abstract
- Description
- Claims
- Application Information
AI Technical Summary
Problems solved by technology
Method used
Examples
preparation example Construction
[0020] The preparation process of the neutron-shielding aluminum-based composite material of the present invention specifically includes the following steps:
[0021] (1) Take the raw material powder by the composition ratio of the shielding material;
[0022] (2) A double-cone high-efficiency mixer is used for mixing, and argon protection is poured into the mixing process, and the grinding medium is bearing steel balls;
[0023] (3) Use the cold isostatic pressing method to press the blank. During the cold isostatic pressing process, a rubber jacket is used to isolate the hydraulic medium (anti-wear hydraulic oil) from the powder. The cold isostatic pressing pressure is 100-200 MPa, and the holding time is 10-40min;
[0024] (4) After the blank is repaired into a regular shape, the sheath is prepared by using a pure aluminum sheet, and the cold isostatic pressed blank is put into the sheath;
[0025] (5) Degas the sheathed blank at a temperature of 300-450°C, and when the v...
Embodiment 1
[0029] Configure powder, weigh 1050g aluminum powder, ZrH 2 Powder 300g and Fu 10 B powder 150g. A double-cone high-efficiency mixer is used for mixing. During the mixing process, argon gas protection is poured in, and the grinding medium is bearing steel balls. After mixing, the powder is put into a cold isostatic pressing bag, and pressed into a green body by cold isostatic pressing, with a pressure of 100 MPa and a pressure hold of 10 minutes. Weld the preform sheath with pure aluminum, degas and package at 450°C. Then, hot isostatic pressing is carried out on the blank cover, the isostatic pressing temperature is 490°C, the pressure is 100MPa, and the pressure is maintained for 4 hours, the pure aluminum cover is removed, and the aluminum matrix composite material is obtained. The density of the material reaches the theoretical density. More than 99%.
Embodiment 2
[0031] Configure powder, weigh 600g of aluminum powder, ZrH 2 Powder 750g and rich 10 B powder 150g. A double-cone high-efficiency mixer is used for mixing. During the mixing process, argon gas protection is poured in, and the grinding medium is bearing steel balls. After mixing, the powder is put into a cold isostatic pressing bag, and is pressed into a green body by cold isostatic pressing at a pressure of 200 MPa, and the pressure is maintained for 40 minutes. Weld the blank sheath with pure aluminum, degas and package at 300°C. Then, hot isostatic pressing is carried out on the blank covering, the isostatic pressing temperature is 520°C, the pressure is 120MPa, and the pressure is kept for 2 hours, the pure aluminum covering is removed, and the aluminum matrix composite material is obtained. The density of the material reaches the theoretical density. More than 98%.
PUM
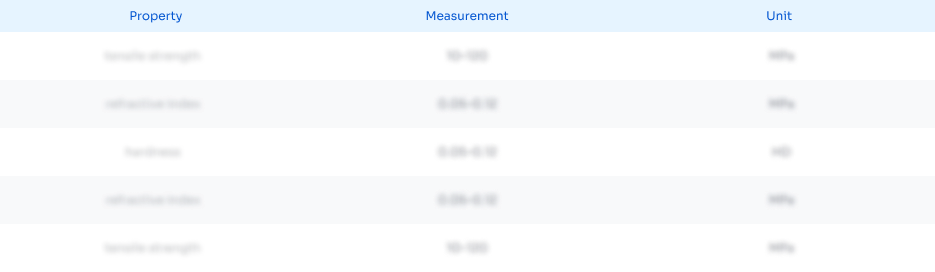
Abstract
Description
Claims
Application Information

- R&D Engineer
- R&D Manager
- IP Professional
- Industry Leading Data Capabilities
- Powerful AI technology
- Patent DNA Extraction
Browse by: Latest US Patents, China's latest patents, Technical Efficacy Thesaurus, Application Domain, Technology Topic, Popular Technical Reports.
© 2024 PatSnap. All rights reserved.Legal|Privacy policy|Modern Slavery Act Transparency Statement|Sitemap|About US| Contact US: help@patsnap.com