Symmetric spatial three-dimensional micro manipulator with three-stage motion amplifying mechanism
A three-dimensional, micro-manipulator technology, applied in the field of micro-nano robots, can solve problems such as limiting the application range of micro-manipulation robots and increasing the difficulty of manipulator motion control, achieving the effects of compact structure, improved motion accuracy, and reduced parasitic displacement
- Summary
- Abstract
- Description
- Claims
- Application Information
AI Technical Summary
Problems solved by technology
Method used
Image
Examples
Embodiment Construction
[0028] The present invention will be described in detail below in conjunction with the accompanying drawings and specific embodiments.
[0029] The structure diagram of the symmetrical three-dimensional micro-manipulator with three-stage motion amplification mechanism of the present invention is as follows: Figure 1-Figure 5 As shown, it consists of a base 1 and a plurality of enlarged clamping modules, and the number of enlarged clamping modules can be determined according to the needs of use. figure 1 It is a structural schematic diagram of an embodiment with four enlarged clamping modules. Each amplifying clamping module includes a piezoelectric ceramic driver 6 , a bridge-type displacement amplifying mechanism 3 , two lever displacement amplifying mechanisms 2 , a Z-beam displacement amplifying mechanism 7 , two flexible guide mechanisms 8 and clamping jaws 4 . The two lever displacement amplifying mechanisms 2 are symmetrically arranged on both sides of the bridge type ...
PUM
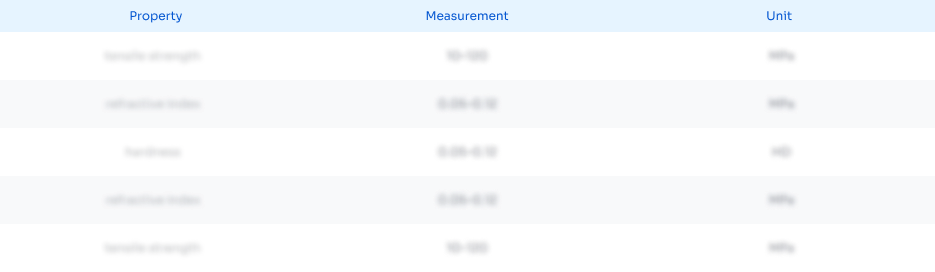
Abstract
Description
Claims
Application Information

- Generate Ideas
- Intellectual Property
- Life Sciences
- Materials
- Tech Scout
- Unparalleled Data Quality
- Higher Quality Content
- 60% Fewer Hallucinations
Browse by: Latest US Patents, China's latest patents, Technical Efficacy Thesaurus, Application Domain, Technology Topic, Popular Technical Reports.
© 2025 PatSnap. All rights reserved.Legal|Privacy policy|Modern Slavery Act Transparency Statement|Sitemap|About US| Contact US: help@patsnap.com