Construction method of assembling-type load-bearing steel structure factory building framework
A construction method and assembled technology, applied in truss structures, building components, building structures, etc., can solve the problems of building waterproof and rainproof performance, deformation and dislocation of the overall structure of the workshop, and large assembly errors of the workshop. Enhance the overall structural strength and bearing capacity, simplify the construction process, and ensure the effect of performance
- Summary
- Abstract
- Description
- Claims
- Application Information
AI Technical Summary
Problems solved by technology
Method used
Image
Examples
Embodiment Construction
[0031] The technical solution of the present invention is further described below, but the scope of protection is not limited to the description.
[0032] Such as Figure 1 to Figure 8 As shown, the present invention provides a construction method for an assembled load-bearing steel structure factory building skeleton, comprising the following steps:
[0033] Step 1: Build the wall frame 1: set up the front and rear wall frames 11 and the left and right wall frames 12 on the ground, so that the front and rear wall frames 11, the left and right wall frames 12 surround and form a closed rectangular wall frame 1 on the ground;
[0034] Step 2: Preparation of hollow roof composite beam frame 2: According to the outer contour size of the wall frame 1 in step 1, several hollow roof composite beam frames 2 are prepared, and the hollow roof composite beam frame 2 consists of two cable-stayed longitudinal beams 21 arranged in parallel and several cable-stayed beams 22 welded between t...
PUM
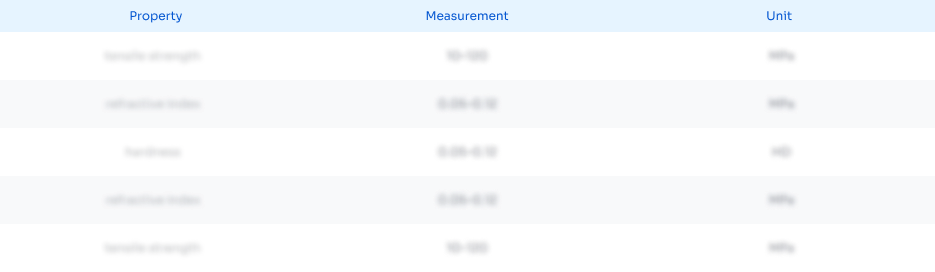
Abstract
Description
Claims
Application Information

- R&D
- Intellectual Property
- Life Sciences
- Materials
- Tech Scout
- Unparalleled Data Quality
- Higher Quality Content
- 60% Fewer Hallucinations
Browse by: Latest US Patents, China's latest patents, Technical Efficacy Thesaurus, Application Domain, Technology Topic, Popular Technical Reports.
© 2025 PatSnap. All rights reserved.Legal|Privacy policy|Modern Slavery Act Transparency Statement|Sitemap|About US| Contact US: help@patsnap.com