Modified composite fiber membrane and layer-by-layer self-assembly method and application thereof
A layer-by-layer self-assembly and composite fiber membrane technology, applied in the field of materials, can solve problems such as low efficiency, long time, environmental pollution, etc., and achieve the effect of expanding the selection range, convenient operation, and expanding the application range
- Summary
- Abstract
- Description
- Claims
- Application Information
AI Technical Summary
Problems solved by technology
Method used
Image
Examples
Embodiment 1
[0030] This embodiment provides a method for self-assembly of modified composite fiber membrane layer by layer, comprising the following steps:
[0031] S1, Preparation of polystyrene micro / nanofibrous membrane (PS) by electrospinning technique.
[0032] Specifically, polystyrene was dissolved in a mixed solution of tetrahydrofuran and N,N-dimethylformamide (mass ratio 1:1) to obtain a 10 wt% polystyrene solution. Then polystyrene micro / nanofiber membrane (PS) was prepared by electrospinning technology, the process parameters were: electrospinning voltage was 20kV, solution flow rate was 1mL / h, receiving distance was 15cm, temperature was 25°C, relative humidity was 40%. Subsequently, the obtained polystyrene micro / nanofiber membrane was vacuum-dried at 60° C. to fully evaporate the remaining solvent.
[0033] S2, Plasma modification of polystyrene micro / nanofiber membrane to obtain a base plate with a large amount of negative charge on the surface (PS O ).
[0034] Specif...
Embodiment 2
[0045] This embodiment provides a method for self-assembly of modified composite fiber membrane layer by layer, comprising the following steps:
[0046] S1, Fabrication of polymethyl methacrylate micro / nanofibrous membranes by electrospinning technique.
[0047] Specifically, polyacrylonitrile was dissolved in a tetrahydrofuran solution to obtain a 10 wt% polyacrylonitrile solution. Then, polymethyl methacrylate micro / nanofiber membranes were prepared by electrospinning technology. The process parameters were as follows: electrospinning voltage was 20kV, solution flow rate was 1mL / h, receiving distance was 15cm, temperature was 25°C, and relative humidity was 40%. Subsequently, the obtained polymethylmethacrylate micro / nanofiber membrane was vacuum-dried at 60° C. to fully volatilize the remaining solvent.
[0048] S2, Plasma modification of polymethyl methacrylate micro / nano fiber membrane to obtain a bottom plate with a large amount of negative charge on the surface.
[0...
Embodiment 3
[0055] This embodiment provides a method for self-assembly of modified composite fiber membrane layer by layer, comprising the following steps:
[0056] S1, Preparation of polyacrylonitrile micro / nanofiber membranes by electrospinning technique.
[0057] Specifically, polyacrylonitrile was dissolved in N,N-dimethylformamide solution to obtain a 10 wt% polyacrylonitrile solution. Then, the polyacrylonitrile micro / nano fiber membrane was prepared by electrospinning technology, and the process parameters were as follows: the electrospinning voltage was 18kV, the solution flow rate was 0.8mL / h, the receiving distance was 15cm, the temperature was 25°C, and the relative humidity was 40%. . Subsequently, the obtained polyacrylonitrile micro / nanofiber membrane was vacuum-dried at 60° C. to fully evaporate the remaining solvent.
[0058] S2, Plasma modification of polyacrylonitrile micro / nanofiber membrane to obtain a bottom plate with a large amount of negative charge on the surfac...
PUM
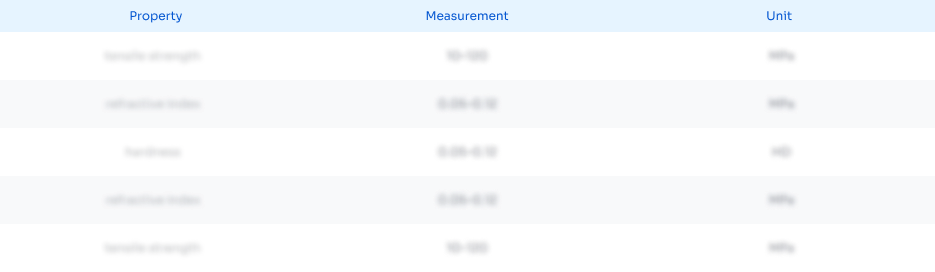
Abstract
Description
Claims
Application Information

- R&D Engineer
- R&D Manager
- IP Professional
- Industry Leading Data Capabilities
- Powerful AI technology
- Patent DNA Extraction
Browse by: Latest US Patents, China's latest patents, Technical Efficacy Thesaurus, Application Domain, Technology Topic, Popular Technical Reports.
© 2024 PatSnap. All rights reserved.Legal|Privacy policy|Modern Slavery Act Transparency Statement|Sitemap|About US| Contact US: help@patsnap.com