Preparation device and method for oxidation resistant coatings on inner walls of boiler header and pipe base
An anti-oxidation coating, boiler header technology, applied in the direction of coating, metal material coating process, solid-state diffusion coating, etc., can solve the problem of insufficient anti-steam oxidation ability, achieve control of vapor deposition rate and exhaust emission, The effect of avoiding tissue degeneration
- Summary
- Abstract
- Description
- Claims
- Application Information
AI Technical Summary
Problems solved by technology
Method used
Image
Examples
preparation example Construction
[0030] A method for preparing an anti-oxidation coating on the inner wall of a boiler header and a pipe seat according to the present invention comprises the following steps:
[0031] 1) Close the second valve 7, open the third to fifth valves 8 to 10 at the same time, use the mechanical pump to evacuate the pipeline system through the first valve 6, and close the first to fourth valves when the vacuum degree of the system is higher than 1000Pa 6-9 and the sixth valve 11;
[0032]2) Turn on the first heating furnace 1, and heat the header, the pipe seat 2 and the penetrating agent tank 3 to be prepared for the inner wall coating at the same time, and keep the heating curve consistent. Set the final heating temperature and holding time according to the material of the header and pipe seat, and the final heating temperature range is 600-950°C;
[0033] 3) During the heating process, the material in the penetrating agent tank 3 is heated and decomposed, and the through hole on t...
Embodiment 1
[0037] Prepare an anti-oxidation coating on the inner wall of the header and pipe seat made of P92, and weld the header and pipe seat that have been degreased and derusted on the inner wall to the pipeline system. After measurement, the area of header and pipe seat 2 to be prepared with inner wall coating is about 20m2 2 , osmosis agent tank 3 is put into 15KG osmosis agent. According to the heat treatment process of P92 material and weld seam, the final heating temperature is 760°C and the holding time is 6h.
[0038] The morphology of the prepared inner wall coating is as follows figure 2 , the distribution of the main elements of the coating see image 3 .
[0039] The weight gain curve of saturated steam oxidation at 650℃ for 500h is shown in Figure 4 .
PUM
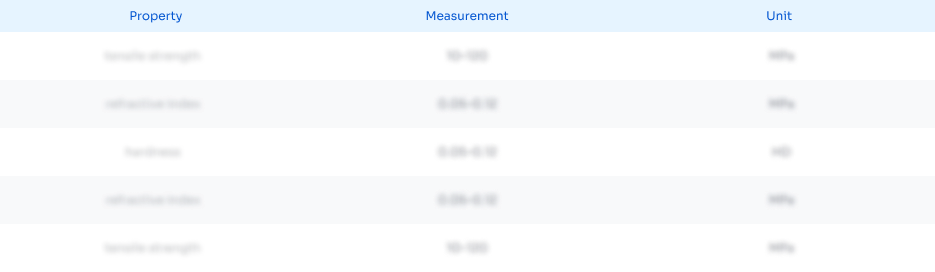
Abstract
Description
Claims
Application Information

- R&D Engineer
- R&D Manager
- IP Professional
- Industry Leading Data Capabilities
- Powerful AI technology
- Patent DNA Extraction
Browse by: Latest US Patents, China's latest patents, Technical Efficacy Thesaurus, Application Domain, Technology Topic, Popular Technical Reports.
© 2024 PatSnap. All rights reserved.Legal|Privacy policy|Modern Slavery Act Transparency Statement|Sitemap|About US| Contact US: help@patsnap.com