A rh furnace refining hydrogen and oxygen control process
A process, hydrogen-oxygen technology, applied in the field of iron and steel smelting, can solve the problems of reduced end face shrinkage and impact toughness, and reduced steel elongation, and achieve the effects of shortening cycle, fast slag formation, and cost reduction
- Summary
- Abstract
- Description
- Claims
- Application Information
AI Technical Summary
Problems solved by technology
Method used
Examples
Embodiment 1
[0027] A RH furnace refining hydrogen and oxygen control process, the process steps are:
[0028] Step (1): Measure the temperature of the molten steel in the ladle, and take a sample to measure the N and C content. As the starting condition of the RH treatment, the ladle is raised to the treatment position so that the riser is inserted into the molten steel. The insertion depth of the riser is 520mm; the initial temperature of RH vacuum cycle degassing treatment is 1580℃;
[0029] Step (2): Vacuum operation, using high-pressure nitrogen and oxygen mixing ratio of 8:2 or argon and oxygen mixing ratio of 8:2 as the lifting gas of the riser steel liquid; control RH according to the measured nitrogen content The vacuum degree is maintained at 3-4.5kPa, the weight content of the main components of the added refining slag is: CaO 57-67%, Al2O3 33%, SiO2 8%, MgO≤2%, TiO2≤0.1%, others are Fe2O3, Fe3O4 The sum of, P and S is less than or equal to 2%; the refining slag is added in 2-3 batc...
Embodiment 2
[0035] A RH furnace refining hydrogen and oxygen control process, the process steps are:
[0036] Step (1): Measure the temperature of the molten steel in the ladle, and take a sample to measure the N and C content. As the starting condition of the RH treatment, the ladle is raised to the treatment position so that the riser is inserted into the molten steel. The insertion depth of the riser is 500-550mm; the initial temperature of RH vacuum cycle degassing treatment is 1580-1590℃;
[0037] Step (2): Vacuum operation, using high-pressure nitrogen and oxygen mixing ratio of 8:2 or argon and oxygen mixing ratio of 8:2 as the lifting gas of the riser steel liquid; control RH according to the measured nitrogen content The vacuum degree is maintained at 3-4.5kPa, the weight content of the main components of the added refining slag is: CaO 58%, Al2O3 33%, SiO2 8%, MgO≤2%, TiO2≤0.1%, others are Fe2O3, Fe3O4, P The sum of S and S is less than or equal to 2%; the refining slag is added in ...
Embodiment 3
[0043] A RH furnace refining hydrogen and oxygen control process, the process steps are:
[0044] Step (1): Measure the temperature of the molten steel in the ladle, and take a sample to measure the N and C content. As the starting condition of the RH treatment, the ladle is raised to the treatment position so that the riser is inserted into the molten steel. The insertion depth of the riser is 500-550mm; the initial temperature of RH vacuum cycle degassing treatment is 1580-1590℃;
[0045] Step (2): Vacuum operation, using high-pressure nitrogen and oxygen mixing ratio of 8:2 or argon and oxygen mixing ratio of 8:2 as the lifting gas of the riser steel liquid; control RH according to the measured nitrogen content The vacuum degree is maintained at 3-4.5kPa, the weight content of the main components of the added refining slag is: CaO 57-67%, Al2O3 33%, SiO2 8%, MgO≤2%, TiO2≤0.1%, others are Fe2O3, Fe3O4 The sum of, P and S is less than or equal to 2%; the refining slag is added in...
PUM
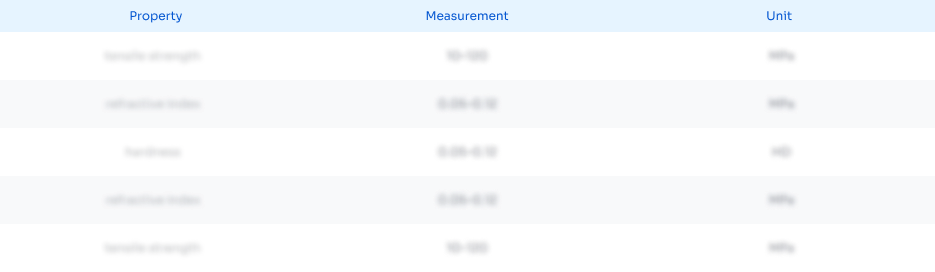
Abstract
Description
Claims
Application Information

- R&D
- Intellectual Property
- Life Sciences
- Materials
- Tech Scout
- Unparalleled Data Quality
- Higher Quality Content
- 60% Fewer Hallucinations
Browse by: Latest US Patents, China's latest patents, Technical Efficacy Thesaurus, Application Domain, Technology Topic, Popular Technical Reports.
© 2025 PatSnap. All rights reserved.Legal|Privacy policy|Modern Slavery Act Transparency Statement|Sitemap|About US| Contact US: help@patsnap.com