A photoinduced shape memory composite material capable of precise recovery and its preparation method
A light-induced shape memory and composite material technology, applied in the field of functional composite materials, can solve the problems of low deformation rate and low deformation recovery rate
- Summary
- Abstract
- Description
- Claims
- Application Information
AI Technical Summary
Problems solved by technology
Method used
Image
Examples
Embodiment 1
[0041] (1) Preparation of sulfonated carbon nanotubes (S-CNT): the suspension obtained after ultrasonication of carbon nanotube (0.25wt%) aqueous solution for 1h was added dropwise to the same volume of p-benzenesulfonic acid (0.46wt%) and super In the hydrochloric acid solution (0.15wt%) of potassium sulfate (0.18wt%), carry out sulfonation under the condition of ice-water bath for 4h, then wash with distilled water and dry;
[0042] (2) Preparation of PU / S-CNT solution: S-CNT DMF solution (0.15wt%) was ultrasonically dispersed for 1 h, then added to the same volume of PU DMF solution (15wt%) and mixed at 80°C for 15 minutes;
[0043] (3) Flocculation of PU / S-CNT composites: Pour the above solution into distilled water and keep stirring to obtain PU / S-CNT flocs, which are washed with distilled water and then dried;
[0044] (4) Preparation of HDPE / PU / S-CNT composite pellets: after crushing the dried PU / S-CNT composite, twin-screw extrusion and granulation with HDPE pellets to...
Embodiment 2
[0048] (1) Preparation of sulfonated carbon nanotubes: The suspension obtained after ultrasonication of carbon nanotube (0.25wt%) aqueous solution for 1h was added dropwise to the same volume containing p-benzenesulfonic acid (0.46wt%) and potassium persulfate (0.18wt%) %) in hydrochloric acid solution (0.15wt%), carry out sulfonation 4h under the condition of ice-water bath, then wash and dry with distilled water;
[0049] (2) Preparation of PU / S-CNT solution: ultrasonically disperse the DMF solution (0.15wt%) of S-CNT for 1 hour, then add it to the same volume of 80°C PU in DMF solution (15wt%) and mix for 15 minutes;
[0050] (3) Flocculation of PU / S-CNT composites: Pour the above solution into distilled water and keep stirring to obtain PU / S-CNT flocs, which are washed with distilled water and then dried;
[0051] (4) Preparation of HDPE / PU / S-CNT composite pellets: after crushing the dried PU / S-CNT composite, twin-screw extrusion and granulation with HDPE pellets to contro...
Embodiment 3
[0055] (1) Preparation of sulfonated carbon nanotubes: The suspension obtained after ultrasonication of carbon nanotube (0.25wt%) aqueous solution for 1h was added dropwise to the same volume containing p-benzenesulfonic acid (0.46wt%) and potassium persulfate (0.18wt%) %) in hydrochloric acid solution (0.15wt%), carry out sulfonation 4h under the condition of ice-water bath, then wash and dry with distilled water;
[0056] (2) Preparation of PU / S-CNT solution: ultrasonically disperse the DMF solution (0.15wt%) of S-CNT for 1 hour, then add it to the same volume of 80°C PU in DMF solution (15wt%) and mix for 15 minutes;
[0057] (3) Flocculation of PU / S-CNT composites: Pour the above solution into distilled water and keep stirring to obtain PU / S-CNT flocs, which are washed with distilled water and then dried;
[0058] (4) Preparation of HDPE / PU / S-CNT composite pellets: after crushing the dried PU / S-CNT composite, twin-screw extrusion and granulation with HDPE pellets to contro...
PUM
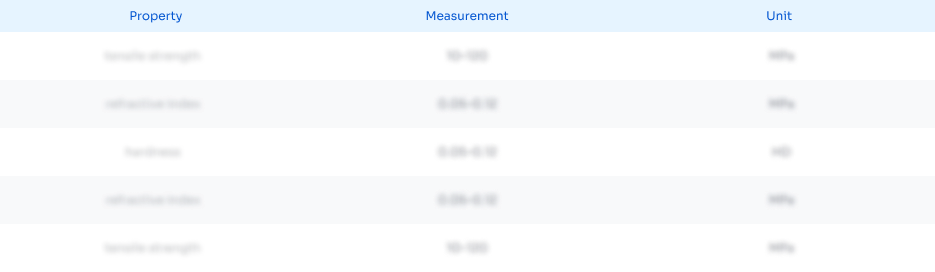
Abstract
Description
Claims
Application Information

- Generate Ideas
- Intellectual Property
- Life Sciences
- Materials
- Tech Scout
- Unparalleled Data Quality
- Higher Quality Content
- 60% Fewer Hallucinations
Browse by: Latest US Patents, China's latest patents, Technical Efficacy Thesaurus, Application Domain, Technology Topic, Popular Technical Reports.
© 2025 PatSnap. All rights reserved.Legal|Privacy policy|Modern Slavery Act Transparency Statement|Sitemap|About US| Contact US: help@patsnap.com