Preparation method of diamond grinding wheel with ordered abrasive materials
A technology of orderly arrangement of diamond grinding wheels, which is applied in the field of hard material products, can solve the problems of inability to achieve orderly arrangement of abrasives, small height of abrasive grains, and short service life of grinding wheels, so as to achieve shortened preparation time, long service life and enhanced grip force effect
- Summary
- Abstract
- Description
- Claims
- Application Information
AI Technical Summary
Problems solved by technology
Method used
Image
Examples
Embodiment 1
[0026] A method for preparing a diamond grinding wheel with ordered abrasives includes the following steps:
[0027] S1: Preparation of the base body: design the drawing of the grinding wheel base body, and use the CNC lathe to process the grinding wheel base body according to the drawing;
[0028] S2: Inkjet: After pretreatment of the grinding wheel substrate, spray ink layer 1 on the substrate, the thickness of ink layer 1 is 0.04mm, and then bake in an oven at 160°C for 10-40 minutes;
[0029] S3: Hole making: using a laser laser engraving machine to engrave blind holes 5 the size of diamond in an orderly arrangement on the upper sand surface. The blind holes 5 have a diameter of 0.3mm, a depth of 0.05mm, and a spacing of 0.4mm; the radium The engraving machine is provided with a positioning device and a rotating device, the positioning device is movably connected to the rotating device, and the positioning device can drive the rotating device to realize positioning and drilling. ...
Embodiment 2
[0035] A method for preparing a diamond grinding wheel with ordered abrasives includes the following steps:
[0036] S1: Preparation of the base body: design the drawing of the grinding wheel base body, and use the CNC lathe to process the grinding wheel base body according to the drawing;
[0037] S2: Inkjet: After pretreatment of the grinding wheel substrate, spray ink layer 1 on the substrate with a thickness of 0.03mm, and then bake it in an oven at 160°C for 10-40 minutes;
[0038] S3: Hole making: use a laser laser engraving machine to engrave blind holes 5 the size of diamond in an orderly arrangement on the upper sand surface. The blind holes 5 are 0.2mm in diameter, 0.03mm in depth, and 0.3mm apart; the radium The engraving machine is provided with a positioning device and a rotating device, the positioning device is movably connected to the rotating device, and the positioning device can drive the rotating device to realize positioning and drilling.
[0039] S4: Electroless ...
Embodiment 3
[0044] A method for preparing a diamond grinding wheel with ordered abrasives includes the following steps:
[0045] S1: Preparation of the base body: design the drawing of the grinding wheel base body, and use the CNC lathe to process the grinding wheel base body according to the drawing;
[0046] S2: Inkjet: After pretreatment of the grinding wheel substrate, spray ink layer 1 on the substrate, the thickness of ink layer 1 is 0.01mm, and then bake in an oven at 160°C for 10-40 minutes;
[0047] S3: Hole making: using a laser laser engraving machine to engrave blind holes 5 the size of diamond in an orderly arrangement on the upper sand surface. The blind holes 5 are 0.1mm in diameter, 0.01mm in depth, and 0.2mm apart; the radium The engraving machine is provided with a positioning device and a rotating device, the positioning device is movably connected to the rotating device, and the positioning device can drive the rotating device to realize positioning and drilling.
[0048] S4: ...
PUM
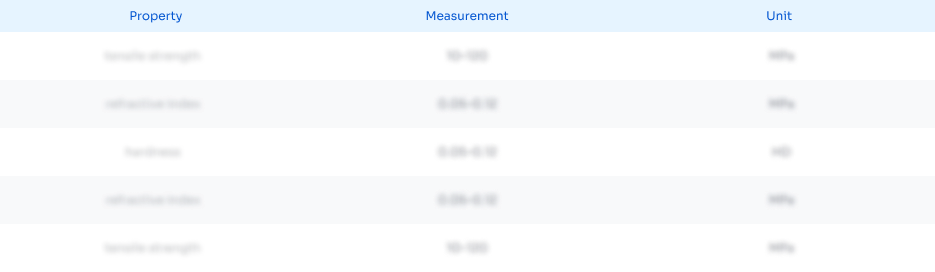
Abstract
Description
Claims
Application Information

- R&D
- Intellectual Property
- Life Sciences
- Materials
- Tech Scout
- Unparalleled Data Quality
- Higher Quality Content
- 60% Fewer Hallucinations
Browse by: Latest US Patents, China's latest patents, Technical Efficacy Thesaurus, Application Domain, Technology Topic, Popular Technical Reports.
© 2025 PatSnap. All rights reserved.Legal|Privacy policy|Modern Slavery Act Transparency Statement|Sitemap|About US| Contact US: help@patsnap.com