Preparation method for titanium niobium nitride nanotube array and nitrided layer composite structure
A nanotube array and composite structure technology is applied in the field of preparation of titanium nitride niobium nanotube arrays and nitriding layer composite structures, which can solve problems such as low cost, achieve complete structure and morphology, increase active sites, and large ratio. The effect of surface area
- Summary
- Abstract
- Description
- Claims
- Application Information
AI Technical Summary
Problems solved by technology
Method used
Image
Examples
Embodiment 1
[0043] Using a titanium-niobium alloy with a titanium content of 20 wt% as a substrate, the polished titanium-niobium alloy was placed in acetone, absolute ethanol and deionized water for ultrasonic cleaning in sequence, and the cleaning time was 10 minutes each time. Then put the titanium-niobium alloy in 75g / L CrO 3 , 100ml / LHF solution polishing solution, the polishing temperature is 40°C, and the polishing time is 5min. Take it out, wash it with plenty of deionized water, and dry it. In the electrolytic cell, the polished, polished and cleaned titanium-niobium alloy is used as the anode, and the graphite electrode is used as the cathode, wherein the electrolyte is a water mixed solution containing 0.5wt% fluorine ions, the anodic oxidation voltage is 20V, and the temperature is 25°C. The time is 15 minutes. The anodized titanium-niobium alloy was heat-treated at a constant temperature of 450°C for 2 hours in an air atmosphere, and then cooled with the furnace. The high ...
Embodiment 2
[0045] Using a titanium-niobium alloy with a titanium content of 60wt% as a substrate, the polished titanium-niobium alloy was placed in acetone, absolute ethanol and deionized water for ultrasonic cleaning in sequence, and the cleaning time was 20 minutes each time. Then put the titanium-niobium alloy in 50g / L CrO 3 , 50ml / LHF solution polishing solution, the polishing temperature is 70°C, and the polishing time is 20min. Take it out, wash it with plenty of deionized water, and dry it. In the electrolytic cell, the polished, polished and cleaned titanium-niobium alloy is used as the anode, and the graphite electrode is used as the cathode, wherein the electrolyte is a 0.5wt% fluorine-containing ethylene glycol mixed solution, the anodic oxidation voltage is 60V, and the temperature is 25 ℃, the time is 3h. The anodized titanium-niobium alloy was heat-treated at a constant temperature of 450°C for 2 hours in an air atmosphere, and then cooled with the furnace. The high-temp...
Embodiment 3
[0047] Using a titanium-niobium alloy with a titanium content of 56wt% as a substrate, the polished titanium-niobium alloy was placed in acetone, absolute ethanol and deionized water for ultrasonic cleaning in sequence, and the cleaning time was 10 minutes each time. Then put the titanium-niobium alloy in 50g / L CrO 3 , 100ml / LHF solution polishing solution, the polishing temperature is 60°C, and the polishing time is 15min. Take it out, wash it with plenty of deionized water, and dry it. In the electrolytic cell, the polished, polished and cleaned titanium-niobium alloy is used as the anode, and the graphite electrode is used as the cathode, wherein the electrolyte is a water mixed solution containing 2.5wt% fluorine ions, the anodic oxidation voltage is 30V, and the temperature is 25°C. The time is 30 minutes. The anodized titanium-niobium alloy was heat-treated at a constant temperature of 450°C for 2.5 hours in an air atmosphere, and then cooled with the furnace. The hig...
PUM
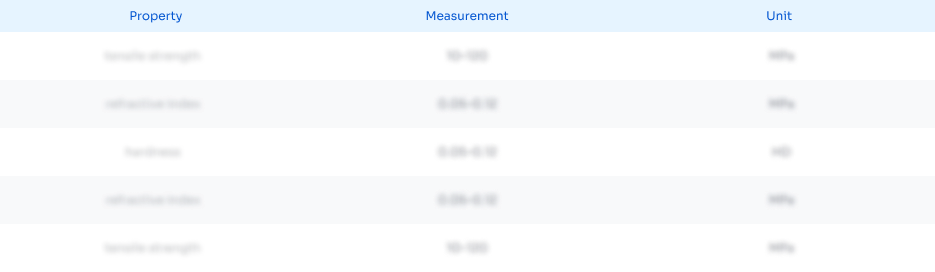
Abstract
Description
Claims
Application Information

- R&D Engineer
- R&D Manager
- IP Professional
- Industry Leading Data Capabilities
- Powerful AI technology
- Patent DNA Extraction
Browse by: Latest US Patents, China's latest patents, Technical Efficacy Thesaurus, Application Domain, Technology Topic, Popular Technical Reports.
© 2024 PatSnap. All rights reserved.Legal|Privacy policy|Modern Slavery Act Transparency Statement|Sitemap|About US| Contact US: help@patsnap.com