Thermoplastic halogen-free low-smoke flame-retardant ceramic polyolefin oxygen barrier material
A polyolefin oxygen barrier, low-smoke and flame-retardant technology, applied in the direction of plastic/resin/wax insulators, organic insulators, etc., can solve the problems of serious threats to high-rise buildings, difficulty in observing fire sources, and difficulty in handling accidents. Small, operational aspects, low price effect
- Summary
- Abstract
- Description
- Claims
- Application Information
AI Technical Summary
Problems solved by technology
Method used
Image
Examples
Embodiment 1
[0020] 100 parts of ethylene-vinyl acetate copolymer weighed in parts by weight, 50 parts of magnesium hydroxide as flame retardant, 25 parts of mica powder as ceramic powder A, 50 parts of kaolin as ceramic powder B, and 50 parts of ceramic powder C as white carbon 25 parts of black, 30 parts of low-melting glass powder as flux, 5 parts of stearic acid as lubricant, 2 parts of coupling agent 11-100, put into internal mixer for mixing, when the temperature reaches 120℃ The material is discharged and fed into the twin-screw extruder through the conical tipping bucket. Zone 120°C, Zone 7 125°C, Zone 8 125°C, Zone 9 125°C. Through single-screw granulation extrusion and cold cutting, a thermoplastic halogen-free low-smoke flame-retardant ceramizable polyolefin oxygen barrier layer material is obtained.
Embodiment 2
[0022] 70 parts of ethylene-vinyl acetate copolymer, 30 parts of polyethylene copolymer, 50 parts of aluminum hydroxide as flame retardant, 70 parts of kaolin as ceramic powder A, 30 parts of white carbon black as ceramic powder B Parts, flux A is 15 parts of low-melting glass powder (melting point 450°C-500°C), flux B is 25 parts of low-melting point glass powder (melting point 850°C-900°C), lubricant is 5 parts of polyethylene wax, even The joint agent is 11-100 3 parts, put into the internal mixer for mixing, when the mixing reaches 125°C, the material is discharged, and the material is fed into the twin-screw extruder through the conical tipping bucket, and the twin-screw temperature zone is set to The first zone is 112°C, the second zone is 118°C, the third zone is 118°C, the fourth zone is 123°C, the fifth zone is 123°C, the sixth zone is 123°C, the seventh zone is 128°C, the eighth zone is 128°C, and the ninth zone is 128°C. Through single-screw granulation extrusion an...
Embodiment 3
[0024] 100 parts of ethylene-vinyl acetate copolymer weighed in parts by weight, flame retardant A is 20 parts of magnesium hydroxide, flame retardant A is 60 parts of aluminum hydroxide, ceramic powder A is 50 parts of quartz powder, ceramic powder B is 20 parts of muscovite, 15 parts of zinc oxide as a flux, 5 parts of polyethylene wax as a lubricant, and 3 parts of coupling agent KH5503, put them into the internal mixer for mixing, and discharge when the mixing temperature reaches 115°C , Feed the material into the twin-screw extruder through the conical tipping bucket. The twin-screw temperature zone is set to 110°C in the first zone, 114°C in the second zone, 114°C in the third zone, 118°C in the fourth zone, 118°C in the fifth zone, and 118 in the sixth zone. ℃, 123℃ in the seventh zone, 123℃ in the eighth zone, and 123℃ in the ninth zone. Through single-screw granulation extrusion and cold cutting, a thermoplastic halogen-free low-smoke flame-retardant ceramizable polyo...
PUM
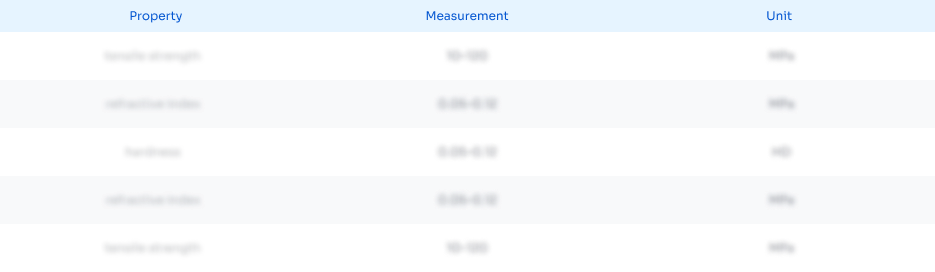
Abstract
Description
Claims
Application Information

- R&D Engineer
- R&D Manager
- IP Professional
- Industry Leading Data Capabilities
- Powerful AI technology
- Patent DNA Extraction
Browse by: Latest US Patents, China's latest patents, Technical Efficacy Thesaurus, Application Domain, Technology Topic, Popular Technical Reports.
© 2024 PatSnap. All rights reserved.Legal|Privacy policy|Modern Slavery Act Transparency Statement|Sitemap|About US| Contact US: help@patsnap.com