A kind of steel truss construction method
A steel truss and construction method technology, which is applied in the processing of building materials, construction, building components, etc., can solve the problem of large gaps at the junction of steel truss slabs and steel columns, not meeting the rapidity of steel structure construction, and difficult manual operation accuracy. Control and other issues, to achieve the effect of reducing the workload on site, improving the phenomenon of slurry leakage, and reducing labor consumption
- Summary
- Abstract
- Description
- Claims
- Application Information
AI Technical Summary
Problems solved by technology
Method used
Image
Examples
Embodiment
[0028] The concrete realization of this embodiment is described in detail below:
[0029] (1) Install steel truss slabs, and use 50×5 angle steel brackets at the junction of steel columns, and the brackets and steel beams are connected by welding.
[0030] During the steel column processing and manufacturing process in the factory, the steel plate support is welded to the steel column according to the floor elevation, so that the steel truss plate support can be completed at one time during the component processing process, and the on-site installation welding angle steel support process is cancelled.
[0031] (2) After the rib truss plate is installed, cut it according to the actual size of the site. After cutting, the gap between the steel column and the truss plate is cut into an L shape with a 0.75mm thick hot-dip galvanized steel plate for sealing
[0032] (3) Studs are used The number of rows is determined by the design according to the beam width. Adjust and optimize ...
PUM
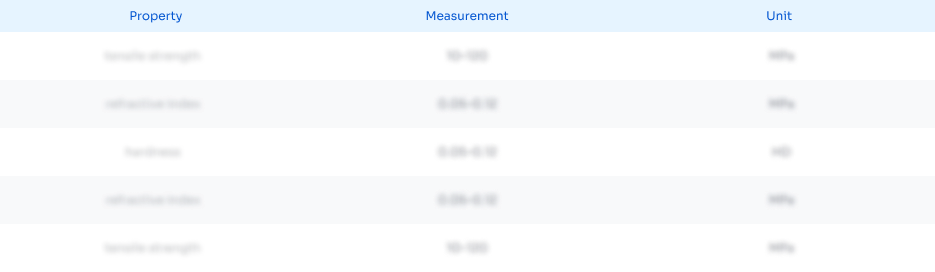
Abstract
Description
Claims
Application Information

- R&D
- Intellectual Property
- Life Sciences
- Materials
- Tech Scout
- Unparalleled Data Quality
- Higher Quality Content
- 60% Fewer Hallucinations
Browse by: Latest US Patents, China's latest patents, Technical Efficacy Thesaurus, Application Domain, Technology Topic, Popular Technical Reports.
© 2025 PatSnap. All rights reserved.Legal|Privacy policy|Modern Slavery Act Transparency Statement|Sitemap|About US| Contact US: help@patsnap.com