Design method of tubular part spin forming spinning roller tracks
A technology of spinning forming and trajectory design, which is applied in computing, special data processing applications, instruments, etc., to achieve the effect of improving production efficiency and shortening forming time
- Summary
- Abstract
- Description
- Claims
- Application Information
AI Technical Summary
Problems solved by technology
Method used
Image
Examples
Embodiment Construction
[0031] The present invention will be further described below in conjunction with the accompanying drawings and specific embodiments.
[0032] The blank 9 in this embodiment is a circular blank, which is a cylindrical piece through spinning. track, etc. In this embodiment, the seven-pass spinning forming of a cylindrical part with an involute wheel track is taken as an example. Based on the above, such as Figure 1 to Figure 4 As shown in , a method for designing the rotary wheel trajectory of cylindrical parts spinning, the specific steps are as follows:
[0033] Taking the mandrel and the blank as the research objects, because during the spinning process, the tail top 10 and the mandrel 8 sandwich the blank and rotate together, and the spinning wheel 12 performs spinning on the blank, and the tail top and the mandrel have the same speed The force is roughly the same as the direction of rotation, but the direction is opposite, so it is only necessary to select the rotary whe...
PUM
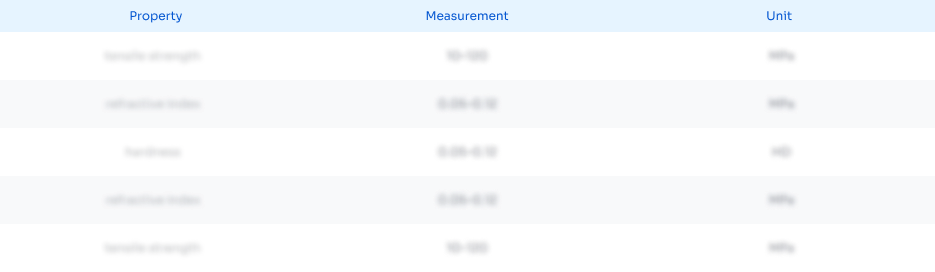
Abstract
Description
Claims
Application Information

- R&D
- Intellectual Property
- Life Sciences
- Materials
- Tech Scout
- Unparalleled Data Quality
- Higher Quality Content
- 60% Fewer Hallucinations
Browse by: Latest US Patents, China's latest patents, Technical Efficacy Thesaurus, Application Domain, Technology Topic, Popular Technical Reports.
© 2025 PatSnap. All rights reserved.Legal|Privacy policy|Modern Slavery Act Transparency Statement|Sitemap|About US| Contact US: help@patsnap.com