Diesel engine exhaust aftertreatment system based on high-chromium stainless steel and treatment method
A high-chromium stainless steel and exhaust after-treatment technology, which is applied in the direction of exhaust treatment, electronic control and electrical control of exhaust treatment devices, can solve the problem that the exhaust after-treatment system is difficult to meet the national VI emission regulations of diesel locomotives, and achieves structural Simple, reduce PM and NOx pollution, optimize the effect of filter structure
- Summary
- Abstract
- Description
- Claims
- Application Information
AI Technical Summary
Problems solved by technology
Method used
Image
Examples
Embodiment 1
[0026] Such as figure 1 As shown, the first embodiment of the present invention provides a diesel engine exhaust aftertreatment system based on high-chromium stainless steel, including:
[0027] Oxidation catalyst 19, particle trap 18 and selective catalytic reduction device 16 arranged in sequence on the exhaust pipeline 3 of diesel engine 8, and several temperature sensors and pressure sensors 2 for detecting temperature and pressure values in various places in the pipeline; The filter element carrier 17 of the particulate trap 18 is a metal fiber braid made of high-temperature-resistant and corrosion-resistant high-chromium stainless steel, and the oxidation catalyst 19 and the particulate trap 18 are integrated to form a continuous regenerative trapping device.
[0028] It also includes the EGR valve 6 located on the connecting pipeline between the intake manifold 10 of the diesel engine 8 and the exhaust manifold 7, the fuel pump / electromagnetic injection valve 11 locat...
Embodiment 2
[0033] This embodiment provides an exhaust gas post-treatment method based on the high-chromium stainless steel-based diesel engine exhaust post-treatment system described in Example 1, and its exhaust pollutant control process is as follows:
[0034] Control the EGR valve 6 and the fuel pump / solenoid injection valve 11 through the control unit 15 to set the EGR rate and fuel injection timing, optimize the internal combustion, and reduce the PM and NO in the exhaust gas as much as possible x content;
[0035] When there is less PM (soot particulate matter) deposition in the diesel particulate filter (DPF) 18, the exhaust gas of the diesel engine 8 first passes through the oxidation catalyst (DOC) 19, CO and HC are being oxidized, and the temperature of the exhaust gas increases, and at the same time NO is oxidized to NOx , its catalytic properties enable PM to be violently oxidized at 200°C in the subsequent particle filter (DPF);
[0036] The pressure inside the DPF is monit...
PUM
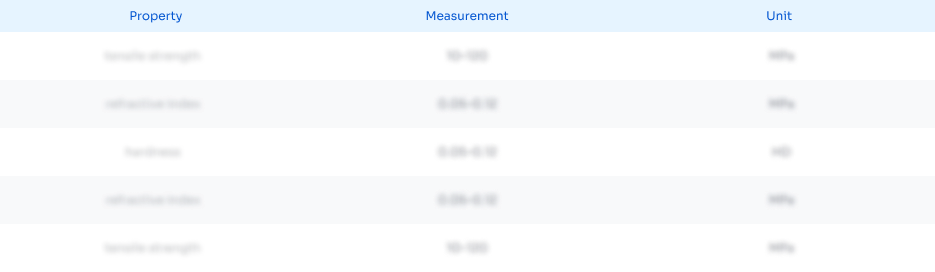
Abstract
Description
Claims
Application Information

- Generate Ideas
- Intellectual Property
- Life Sciences
- Materials
- Tech Scout
- Unparalleled Data Quality
- Higher Quality Content
- 60% Fewer Hallucinations
Browse by: Latest US Patents, China's latest patents, Technical Efficacy Thesaurus, Application Domain, Technology Topic, Popular Technical Reports.
© 2025 PatSnap. All rights reserved.Legal|Privacy policy|Modern Slavery Act Transparency Statement|Sitemap|About US| Contact US: help@patsnap.com