Fire-polishing blackening preparation method of anti-halation step-like glass
A fire polishing and step technology is applied in the field of fire polishing and blackening preparation of anti-halation step glass, which can solve the problems of large difference in thickness of black glass layer, inconsistent thinning amount, thinning of black glass layer, etc. The time required for blackening, the blackening cycle is accelerated, and the processing time is short.
- Summary
- Abstract
- Description
- Claims
- Application Information
AI Technical Summary
Problems solved by technology
Method used
Image
Examples
Embodiment 1
[0040] After the anti-halation stepped glass blank is formed, it is placed in a closed high-temperature furnace with a reducing atmosphere, and 99.99% H 2 ; by controlling H 2 The pressure reducing valve at the gas source maintains the gas pressure in the reducing atmosphere furnace at a slight positive pressure of 0.01-0.02MPa, and the gas flow rate is controlled within the range of 0.2L / min-1L / min; the furnace temperature is first raised from room temperature to 500 ℃, and keep warm at 500℃ for 2-4 hours to completely decompose and volatilize the impurities on the surface of the blank, because the impurities on the glass surface will occupy the surface position and form a high surface barrier, so the impurities on the surface must be removed to ensure the prevention The surface of the halo step glass blank reaches atomic level cleanliness; secondly, the temperature is raised from 500°C to the temperature required for blackening, and kept for a period of time, the blackening ...
Embodiment 2
[0042] After the anti-halation stepped glass blank is formed, it is placed in a closed high-temperature furnace with a reducing atmosphere, and 99.99% H 2 ; by controlling H 2 The pressure reducing valve at the gas source maintains the gas pressure in the reducing atmosphere furnace at a slight positive pressure of 0.01-0.02MPa, and the gas flow rate is controlled within the range of 0.2L / min-1L / min; the temperature of the reducing atmosphere furnace first changes from room temperature Raise the temperature to 200°C and keep it warm at 200°C for 2-4 hours to volatilize the water molecules and other impurities that are easy to desorb on the surface of the glass blank, and with the H 2 Then, the temperature is raised from 200°C to 500°C, and the holding time at 500°C is 2 to 4 hours, so that the impurities on the surface of the blank are completely decomposed and volatilized, ensuring that the surface of the anti-halation step glass blank reaches atomic level cleanliness; again ...
Embodiment 3
[0044] After the anti-halation stepped glass blank is formed, it is placed in a closed high-temperature furnace with a reducing atmosphere, and 99.99% H 2 ; by controlling H 2 The pressure reducing valve at the gas source maintains the gas pressure in the reducing atmosphere furnace at a slight positive pressure of 0.01-0.02MPa, and the gas flow rate is controlled within the range of 0.2L / min-1L / min; the temperature of the reducing atmosphere furnace first changes from room temperature Raise the temperature to 200°C and keep it at 200°C for 2-4 hours; then raise the temperature from 200°C to 500°C and keep it at 500°C for 2-4 hours to completely decompose and volatilize the impurities on the surface of the anti-halation step glass blank; again from 500 ℃ to the temperature required for blackening, and keep it warm for a period of time, the blackening temperature is 550°C ~ 650°C, and the blackening time is 100h ~ 150h; finally, heat up from the blackening temperature to the fi...
PUM
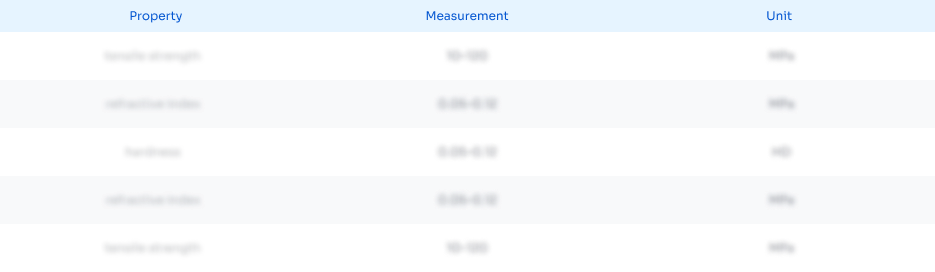
Abstract
Description
Claims
Application Information

- R&D Engineer
- R&D Manager
- IP Professional
- Industry Leading Data Capabilities
- Powerful AI technology
- Patent DNA Extraction
Browse by: Latest US Patents, China's latest patents, Technical Efficacy Thesaurus, Application Domain, Technology Topic, Popular Technical Reports.
© 2024 PatSnap. All rights reserved.Legal|Privacy policy|Modern Slavery Act Transparency Statement|Sitemap|About US| Contact US: help@patsnap.com