Alloying and smelting method of vanadium-containing titanium steel for automobile
A smelting method and steel alloy technology, which is applied in the field of vanadium-containing titanium steel alloy smelting for automobiles, can solve the problems of high production cost of vanadium-containing titanium steel, achieve the effects of shortening the production cycle, improving strong plasticity, and improving the quality of molten steel
- Summary
- Abstract
- Description
- Claims
- Application Information
AI Technical Summary
Problems solved by technology
Method used
Image
Examples
Embodiment 1
[0036] Reference attached figure 1 The flow chart of the embodiment of the present invention provides a method for alloying and smelting vanadium-containing titanium steel for automobiles, comprising the following steps:
[0037] Step a, place 20kg bagged desulfurizer and 40kg bagged dephosphorizer on the bottom of the empty ladle;
[0038] Step b. Pour 13 tons of vanadium-titanium molten iron into a ladle with desulfurizer and dephosphorization agent, and transport it to the converter taphole for standby; wherein, the chemical composition weight percentage of the vanadium-titanium molten iron is as follows: C: 4.0%, V: 0.22%, Ti: 0.15%, P: 0.05%, S: 0.04%, the rest is iron and unavoidable impurities, the temperature is 1310°C;
[0039] Step c, continue to smelt the remaining vanadium-titanium-containing molten iron through the converter, regardless of the vanadium extraction effect, control the chemical composition weight percentage of the molten steel composition at the end...
Embodiment 2
[0043] Reference attached figure 1 The flow chart of the embodiment of the present invention provides a method for alloying and smelting vanadium-containing titanium steel for automobiles, comprising the following steps:
[0044] Step a, place 50kg bagged desulfurizer and 80kg bagged dephosphorizer on the bottom of the empty ladle;
[0045] Step b. Pour 17 tons of vanadium-titanium molten iron into a ladle with desulfurizer and dephosphorization agent, and transport it to the converter taphole for standby; wherein, the chemical composition weight percentage of the vanadium-titanium molten iron is as follows: C: 4.6%, V : 0.30%, Ti: 0.3%, P: 0.068%, S: 0.057%, the rest is iron and unavoidable impurities, the temperature is 1390 ℃;
[0046] Step c, continue to smelt the remaining vanadium-titanium-containing molten iron through the converter, regardless of the vanadium extraction effect, control the chemical composition weight percentage of the molten steel composition at the e...
Embodiment 3
[0050] Reference attached figure 1 The flow chart of the embodiment of the present invention provides a method for alloying and smelting vanadium-containing titanium steel for automobiles, comprising the following steps:
[0051] Step a, place 35kg bagged desulfurizer and 60kg bagged dephosphorizer on the bottom of the empty ladle;
[0052] Step b. Pour 15 tons of vanadium-titanium molten iron into a ladle with desulfurizer and dephosphorization agent, and transport it to the converter taphole for standby; wherein, the chemical composition weight percentage of the vanadium-titanium molten iron is as follows: C: 4.3%, V : 0.26%, Ti: 0.22%, P: 0.06%, S: 0.05%, the rest is iron and unavoidable impurities, the temperature is 1350 ℃;
[0053] Step c, continue to smelt the remaining vanadium-titanium-containing molten iron through the converter, regardless of the vanadium extraction effect, control the chemical composition weight percentage of the molten steel composition at the en...
PUM
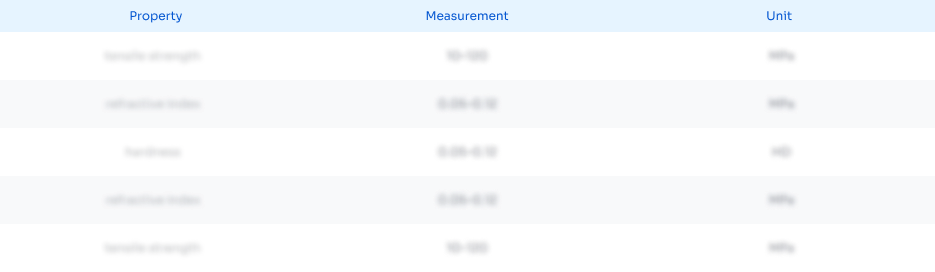
Abstract
Description
Claims
Application Information

- R&D
- Intellectual Property
- Life Sciences
- Materials
- Tech Scout
- Unparalleled Data Quality
- Higher Quality Content
- 60% Fewer Hallucinations
Browse by: Latest US Patents, China's latest patents, Technical Efficacy Thesaurus, Application Domain, Technology Topic, Popular Technical Reports.
© 2025 PatSnap. All rights reserved.Legal|Privacy policy|Modern Slavery Act Transparency Statement|Sitemap|About US| Contact US: help@patsnap.com