Transverse-triangular double-layer structure 4D printing method based on temperature response
A two-layer structure, temperature response technology, applied in 3D object support structure, additive manufacturing, processing data acquisition/processing, etc., can solve the problems of complexity, too slow molding speed, extremely high requirements for workpiece processing equipment, etc., and achieve fast molding speed. , shorten the manufacturing cycle, and achieve the effect of integrated manufacturing
- Summary
- Abstract
- Description
- Claims
- Application Information
AI Technical Summary
Problems solved by technology
Method used
Image
Examples
Embodiment 1
[0061] (1) First, use 3D modeling software to establish a 3D model of a double-layer workpiece that uses polymers for 4D printing. The size of the product workpiece is 10*40*1.5mm 3 , the deformation of the workpiece is intended to have a transverse strain of 0.32 and a longitudinal strain of 0.12.
[0062] (2) Select polylactic acid as the shape memory material for 3D printing, use slicing software to slice the 3D model layer by layer, and set the printing layer height and printing line width according to the desired deformation. The selected line width is 0.4mm, the selected layer height is 50μm. The upper layer of the workpiece uses 150 single-layer horizontal grain patterns with a printing angle of 90°, and the lower layer uses 150 single-layer triangular patterns with three crossing angles of 60° and printing angles of 0°, 60° and 120° respectively. pattern, such as Figure 8 As shown, the thickness ratio of the two layers is 1:1, and the layered slice processing result...
Embodiment 2
[0066] (1) First, use 3D modeling software to establish a 3D model of a double-layer workpiece that uses polymers for 4D printing. The size of the product workpiece is 10*40*1.5mm 3 , the deformation of the workpiece is intended to have a transverse strain of 0.22 and a longitudinal strain of 0.20.
[0067] (2) Select polylactic acid as the shape memory material for 3D printing, use slicing software to slice the 3D model layer by layer, and set the printing layer height and printing line width according to the desired deformation. The selected line width is 0.4mm, the selected layer height is 50μm. The upper layer of the workpiece uses 150 single-layer horizontal grain patterns with a printing angle of 45°, and the lower layer uses 150 single-layer triangular patterns with three crossing angles of 60° and printing angles of 0°, 60° and 120° respectively. pattern, such as Figure 10 As shown, the thickness ratio of the two layers is 1:1, and the layered slice processing resul...
Embodiment 3
[0071] (1) First, use 3D modeling software to establish a 3D model of a double-layer workpiece that uses polymers for 4D printing. The size of the product workpiece is 10*40*1.5mm 3 , the deformation of the workpiece is intended to have a transverse strain of -0.21 and a longitudinal strain of -0.11.
[0072] (2) Select polylactic acid as the shape memory material for 3D printing, use slicing software to slice the 3D model layer by layer, and set the printing layer height and printing line width according to the desired deformation. The selected line width is 0.4mm, the selected layer height is 50μm. The upper layer of the workpiece uses 150 single-layer horizontal grain patterns with a printing angle of 0°, and the lower layer uses 150 single-layer triangular patterns with three crossing angles of 60° and printing angles of 0°, 60° and 120° respectively. pattern, such as Figure 12 , the thickness ratio of the two layers is 1:1, and the layered slice processing results and ...
PUM
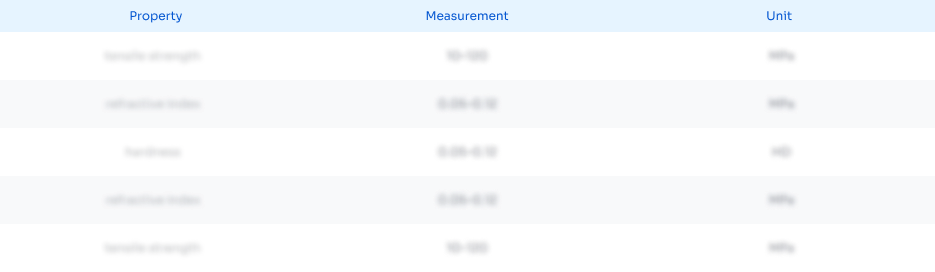
Abstract
Description
Claims
Application Information

- R&D
- Intellectual Property
- Life Sciences
- Materials
- Tech Scout
- Unparalleled Data Quality
- Higher Quality Content
- 60% Fewer Hallucinations
Browse by: Latest US Patents, China's latest patents, Technical Efficacy Thesaurus, Application Domain, Technology Topic, Popular Technical Reports.
© 2025 PatSnap. All rights reserved.Legal|Privacy policy|Modern Slavery Act Transparency Statement|Sitemap|About US| Contact US: help@patsnap.com