Pressure-resistant sintered brick
A sintered brick and pressure-resistant technology, applied in the field of pressure-resistant sintered bricks, can solve the problems of poor balance of internal mechanical properties and poor pressure resistance, and achieve the effect of improving internal strength, high surface activity and reducing agglomeration
- Summary
- Abstract
- Description
- Claims
- Application Information
AI Technical Summary
Problems solved by technology
Method used
Examples
preparation example Construction
[0029] The preparation method of composite brick base material comprises the steps:
[0030] (1) In terms of parts by mass, take 10~20 parts of vermiculite, 30~50 parts of potassium feldspar, 40~60 parts of bauxite, 10~15 parts of fly ash, 12~25 parts of pretreated blast furnace slag, 70~100 parts of coating liquid, first take vermiculite, potassium feldspar, bauxite, fly ash, pretreated blast furnace slag and mix them in a pulverizer, crush them through a 150-mesh sieve to get the sieved material, take the sieved material on the sugar coating machine, spray the coating solution into the sugar coating machine through an atomizer, mix and granulate to obtain granules, take the granules and dry them in an oven at 70~90°C to constant weight to obtain dry matter, take the dry matter in a sintering furnace, and pass through Under nitrogen protection, the temperature is programmed to rise to 1450-1600°C at a rate of 6-10°C / min, heat-preserved and sintered for 3-5 hours, cooled to ro...
PUM
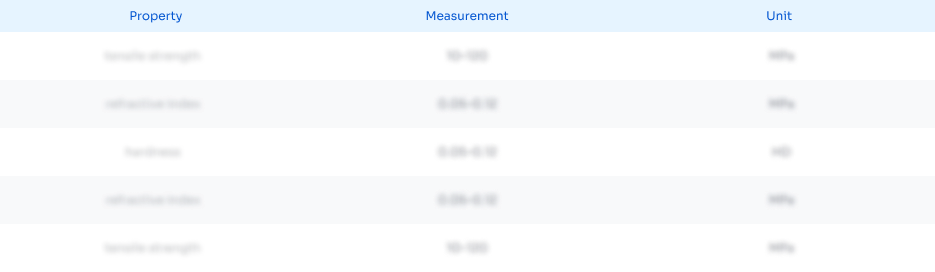
Abstract
Description
Claims
Application Information

- Generate Ideas
- Intellectual Property
- Life Sciences
- Materials
- Tech Scout
- Unparalleled Data Quality
- Higher Quality Content
- 60% Fewer Hallucinations
Browse by: Latest US Patents, China's latest patents, Technical Efficacy Thesaurus, Application Domain, Technology Topic, Popular Technical Reports.
© 2025 PatSnap. All rights reserved.Legal|Privacy policy|Modern Slavery Act Transparency Statement|Sitemap|About US| Contact US: help@patsnap.com