Fast in-situ molding method for conductive fiber reinforced composite material
A technology of reinforced composite materials and conductive fibers, applied in the field of composite material molding, can solve problems such as uneven temperature, poor molding quality, and large thermal stress of parts, so as to improve production efficiency, improve molding quality, and improve stress distribution of finished products Effect
- Summary
- Abstract
- Description
- Claims
- Application Information
AI Technical Summary
Problems solved by technology
Method used
Image
Examples
example 1
[0031] This embodiment is applied in the automatic laying and in-situ molding of continuous carbon fiber reinforced thermosetting resin-based composite materials. The continuous carbon fiber reinforced resin-based composite raw material UIN10000 is a prepreg system with carbon fiber as a reinforcement and epoxy resin cured at a medium temperature as a matrix. The prepreg to be formed is equipped with a laying head through the laying machine, moves on the three-dimensional curved surface mold and lays the material on the surface of the mold, and simultaneously performs the rapid in-situ forming method proposed by the present invention during the laying process. After the laying is completed, the cross-linking and curing are also completed at the same time, realizing the rapid in-situ molding process. The specific operation steps are as follows:
[0032] Step 1: Clean the surface of the mold to be laid: use alcohol, acetone and other organic solvents to clean the surface of the...
example 2
[0039] This embodiment is an application in the winding in-situ forming of the continuous conductive fiber reinforced thermosetting resin-based composite cylinder part. The continuous conductive fiber-reinforced resin-based composite material is a composite material in which carbon fiber is used as a continuous conductive fiber reinforcement and thermosetting phenolic resin is used as a matrix. The thermosetting composite material to be formed is a carbon fiber prepreg, and after being heated to a certain temperature, the phenolic resin coated on the surface of the carbon fiber undergoes a cross-linking chemical reaction with the carbon fiber, so that the carbon fiber prepreg is cured. The carbon fiber prepreg roll with a width of 10mm and a thickness of 0.1mm is used as a raw material, and the cylinder is formed and manufactured by a wet winding machine. According to the curing characteristic curve of thermosetting phenolic resin, 5 temperature gradients can be set to heat th...
PUM
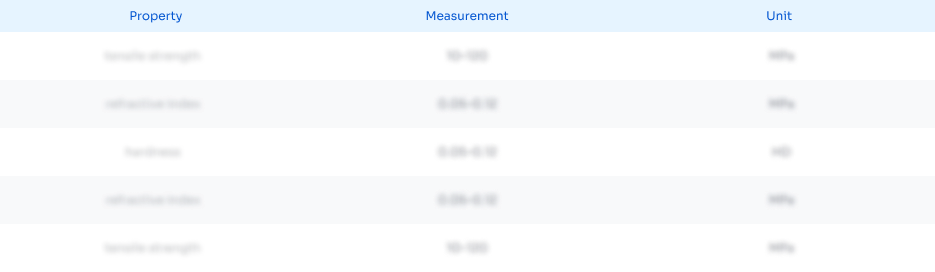
Abstract
Description
Claims
Application Information

- R&D Engineer
- R&D Manager
- IP Professional
- Industry Leading Data Capabilities
- Powerful AI technology
- Patent DNA Extraction
Browse by: Latest US Patents, China's latest patents, Technical Efficacy Thesaurus, Application Domain, Technology Topic, Popular Technical Reports.
© 2024 PatSnap. All rights reserved.Legal|Privacy policy|Modern Slavery Act Transparency Statement|Sitemap|About US| Contact US: help@patsnap.com