Process for producing cathode copper by low-grade anode plates
A kind of anode plate, low-grade technology, applied in the direction of photography technology, photography auxiliary technology, process efficiency improvement, etc., can solve the problems of large environmental pollution, reduce anode mud, long time consumption, etc., to achieve smooth surface, clear and dense lines, The effect of reducing production costs
- Summary
- Abstract
- Description
- Claims
- Application Information
AI Technical Summary
Problems solved by technology
Method used
Examples
Embodiment 1
[0018] The technological scheme of the present invention is: the low-grade, high nickel, tin black copper anode plate containing 75-85% of copper, 5-10% of nickel, and 5-10% of tin, which does not contain precious metals, is not passed through the anode furnace The anode plate is directly cast as the anode and the cathode plate is a pure copper starting plate, and the qualified cathode copper product is obtained by direct electrolytic refining.
[0019] Electrolyte composition used in electrolytic refining: Cu 2+ 42g / L, H 2 SO 4 155g / L, the additives are bone glue 60g / t copper, casein 30g / t copper, modified polyacrylamide 8g / t copper, thiourea 40g / t copper, hydrochloric acid 500ml / t copper, the current intensity is 5000A, and the current density is 100A / ㎡, the cell voltage is 0.25V, the electrolyte temperature is 63°C, the electrolyte circulation flow rate is 30L / min, and the center distance of the same pole is 110mm; during electrolysis, the copper and nickel metal elements...
Embodiment 2
[0024] The technological scheme of the present invention is: the low-grade, high nickel, tin black copper anode plate containing 75-85% of copper, 5-10% of nickel, and 5-10% of tin, which does not contain precious metals, is not passed through the anode furnace The directly cast anode plate is used as the anode, and the cathode plate is a pure copper starting plate, and the qualified cathode copper product is obtained by direct electrolytic refining.
[0025] Electrolyte composition used in electrolytic refining: Cu 2+ 38g / L, H 2 SO 4 160g / L, the additives are bone glue 55g / t copper, casein 28g / t copper, modified polyacrylamide 10g / t copper, thiourea 38g / t copper, hydrochloric acid 480ml / t copper, the current intensity is 6000A, and the current density is 85A / ㎡, the cell voltage is 0.40V, the electrolyte temperature is 60°C, the electrolyte circulation flow rate is 25L / min, and the center distance of the same pole is 110mm; during electrolysis, the copper and nickel metal el...
Embodiment 3
[0030] The technological scheme of the present invention is: the low-grade, high nickel, tin black copper anode plate containing 75-85% of copper, 5-10% of nickel, and 5-10% of tin, which does not contain precious metals, is not passed through the anode furnace The anode plate is directly cast as the anode and the cathode plate is a pure copper starting plate, and the qualified cathode copper product is obtained by direct electrolytic refining.
[0031] Electrolyte composition used in electrolytic refining: Cu 2+ 45g / L, H 2 SO 4 150g / L, the additives are bone glue 65g / t copper, casein 35g / t copper, modified polyacrylamide 6g / t copper, thiourea 42g / t copper, hydrochloric acid 520ml / t copper, the current intensity is 4000A, and the current density is 120A / ㎡, the cell voltage is 0.15V, the electrolyte temperature is 67°C, the electrolyte circulation flow rate is 35L / min, and the center distance of the same pole is 110mm; during electrolysis, the copper and nickel metal elements...
PUM
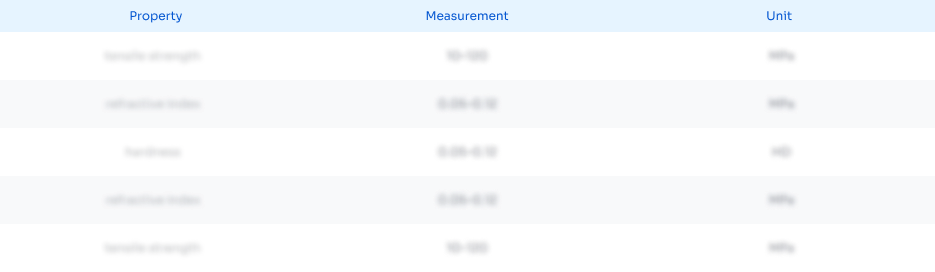
Abstract
Description
Claims
Application Information

- R&D
- Intellectual Property
- Life Sciences
- Materials
- Tech Scout
- Unparalleled Data Quality
- Higher Quality Content
- 60% Fewer Hallucinations
Browse by: Latest US Patents, China's latest patents, Technical Efficacy Thesaurus, Application Domain, Technology Topic, Popular Technical Reports.
© 2025 PatSnap. All rights reserved.Legal|Privacy policy|Modern Slavery Act Transparency Statement|Sitemap|About US| Contact US: help@patsnap.com