A speed cooperative control method for an electronic reciprocating cross-winding system
A cross-winding, collaborative control technology, applied in electric speed/acceleration control, thin material handling, conveying filamentous materials, etc. The quality of the package package, affecting the unwinding performance, etc., achieves the effect of good dynamic follow-up, excellent overall synchronization performance, and improved operation stability
- Summary
- Abstract
- Description
- Claims
- Application Information
AI Technical Summary
Problems solved by technology
Method used
Image
Examples
Embodiment Construction
[0037]The present invention will be further described below in conjunction with the accompanying drawings and preferred embodiments.
[0038] The electronic reciprocating cross-winding system of the present invention at least includes a winding motor 6, a winding motor position encoder 11, a winding motor controller 13, a winding motor driver 5, a traverse motor 10, and a traverse motor position encoder 12. Traverse motor controller 16, traverse motor driver 9, upper computer 23, communication module 24, power supply module 26, power failure storage module 22, diameter sensor 19 and signal input and output module 25, such as figure 1 shown.
[0039] Further, the winding motor 6 can be any type of AC asynchronous motor, brushless DC motor and permanent magnet synchronous motor. As a preferred embodiment, the winding motor 6 adopts a low-cost three-phase AC asynchronous motor.
[0040] Further, the traverse motor 10 can be any type of a small inertia stepping motor or an ultra-...
PUM
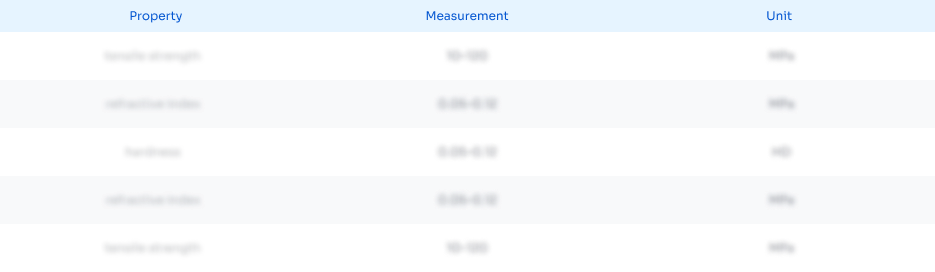
Abstract
Description
Claims
Application Information

- Generate Ideas
- Intellectual Property
- Life Sciences
- Materials
- Tech Scout
- Unparalleled Data Quality
- Higher Quality Content
- 60% Fewer Hallucinations
Browse by: Latest US Patents, China's latest patents, Technical Efficacy Thesaurus, Application Domain, Technology Topic, Popular Technical Reports.
© 2025 PatSnap. All rights reserved.Legal|Privacy policy|Modern Slavery Act Transparency Statement|Sitemap|About US| Contact US: help@patsnap.com