Stirring head and its welding process for friction stir welding of aluminum alloy with large gap
A friction stir welding and stirring head technology, which is applied in welding equipment, metal processing equipment, manufacturing tools, etc., can solve the problems of inconsistent matching gaps of battery boxes, easy to produce defects, etc., to reduce assembly accuracy requirements, promote metal flow, The effect of broadening application prospects
- Summary
- Abstract
- Description
- Claims
- Application Information
AI Technical Summary
Problems solved by technology
Method used
Image
Examples
Embodiment 1
[0041] The thickness of the plate is 2.5mm, the distance between the shoulders of the stirring head is 10mm, the diameter of the stirring needle is 8mm, the ratio of the diameter of the stirring needle to the diameter of the shoulder is 0.8, the length of the stirring needle is 2.3mm, and the distance between the shoulders of the stirring head is 10mm. There are 3 counterclockwise table-building vortex patterns, and 2 spiral grooves are arranged on the stirring needle.
[0042] The specific steps are as follows:
[0043] Step 1: Clean the 2.5mm thick aluminum alloy with alcohol to clean the surface of the metal plate and the oil and oxides on the interface and other substances that hinder the welding process. Place the cleaned plate on the workbench and pass it through the pressure plate and other tools Fix the plate on the workbench, and select a stirring head with a stirring pin length of 2.3 mm according to the thickness of the plate to be welded.
[0044]Step 2: Move the ...
Embodiment 2
[0048] The thickness of the selected plate and the size of the stirring pin are the same as in Example 1.
[0049] The specific implementation steps are as follows:
[0050] Step 1: Clean the 2.5mm thick aluminum alloy with alcohol to clean the surface of the metal plate and the oil and oxides on the interface and other substances that hinder the welding process. Place the cleaned plate on the workbench and pass it through the pressure plate and other tools Fix the plate on the workbench, and select a stirring head with a stirring pin length of 2.3 mm according to the thickness of the plate to be welded.
[0051] Step 2: Move the stirring head to the starting position of the weld, adjust the position of the stirring head so that the center of the stirring needle coincides with the center line of the weld, and move the stirring head down until the end surface of the stirring needle contacts the surface of the workpiece and stop.
[0052] Step 3: Set the welding parameters, the...
Embodiment 3
[0055] The thickness of the selected plate and the size of the stirring pin are the same as in Example 1.
[0056] The specific implementation steps are as follows:
[0057] Step 1: Clean the 2.5mm thick aluminum alloy with alcohol to clean the surface of the metal plate and the oil and oxides on the interface and other substances that hinder the welding process. Place the cleaned plate on the workbench and pass it through the pressure plate and other tools Fix the plate on the workbench, and select a stirring head with a stirring pin length of 2.3 mm according to the thickness of the plate to be welded.
[0058] Step 2: Move the stirring head to the starting position of the weld, adjust the position of the stirring head so that the center of the stirring needle coincides with the center line of the weld, and move the stirring head down until the end surface of the stirring needle contacts the surface of the workpiece and stop.
[0059] Step 3: Set the welding parameters, the...
PUM
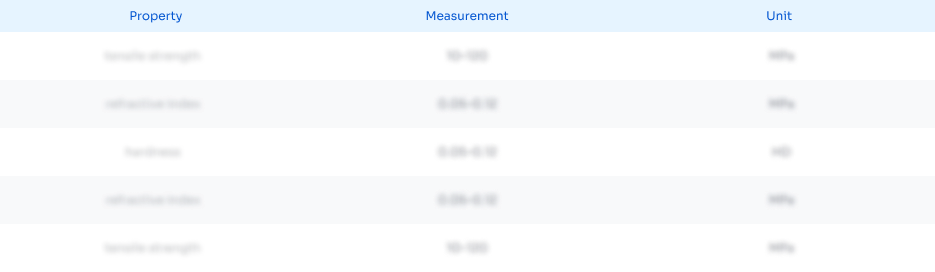
Abstract
Description
Claims
Application Information

- R&D
- Intellectual Property
- Life Sciences
- Materials
- Tech Scout
- Unparalleled Data Quality
- Higher Quality Content
- 60% Fewer Hallucinations
Browse by: Latest US Patents, China's latest patents, Technical Efficacy Thesaurus, Application Domain, Technology Topic, Popular Technical Reports.
© 2025 PatSnap. All rights reserved.Legal|Privacy policy|Modern Slavery Act Transparency Statement|Sitemap|About US| Contact US: help@patsnap.com