A device and method capable of improving coil strength and electromagnetic forming efficiency
An electromagnetic forming and coil strength technology, applied in the field of electromagnetic pulse forming, can solve problems such as low coil strength, energy loss, and coil failure, and achieve the effects of improving forming efficiency, suppressing deformation, and increasing coil strength
- Summary
- Abstract
- Description
- Claims
- Application Information
AI Technical Summary
Problems solved by technology
Method used
Image
Examples
Embodiment 1
[0038] Such as Figure 4 As shown, a device that can improve coil strength and electromagnetic forming efficiency includes a coil metal wire 1, an insulator 2 and a metal groove 3, the coil metal wire 1 is embedded in the metal groove 3, and the insulator 2 is filled in the coil metal wire 1 In the gap between the metal groove 3 and the metal groove 3, the metal workpiece 5 to be formed is placed above the coil metal wire 1.
[0039] In this embodiment, the metal groove 3 is a continuous integral structure, and the coil metal wire 1 is placed in the metal groove 3 .
[0040] In this embodiment, the coil metal wire 1 is a single-layer structure of metal block wire cutting or wire winding.
[0041] In this embodiment, the electrical conductivity of the metal groove 3 is 1e-8˜1e-6 s / m.
[0042] In this embodiment, the height of the metal groove 3 is greater than that of the insulator 2 .
[0043] A method that can improve coil strength and electromagnetic forming efficiency, u...
Embodiment 2
[0047] Such as Figure 5 As shown, the difference between the device of this embodiment and the device of Embodiment 1 is that in this embodiment, the height of the metal groove 3 is lower than that of the insulator 2, and the rest of the structure and forming method are the same as in Embodiment 1.
Embodiment 3
[0049] Such as Figure 6 As shown, the difference between the device of this embodiment and the device of Embodiment 1 is that in this embodiment, the height of the metal groove 3 is flush with the height of the insulator 2, and the coil metal wire 1 is wire-cut or wound from a metal block. The multilayer coil structure, all the other structures and forming method are the same as embodiment 1.
PUM
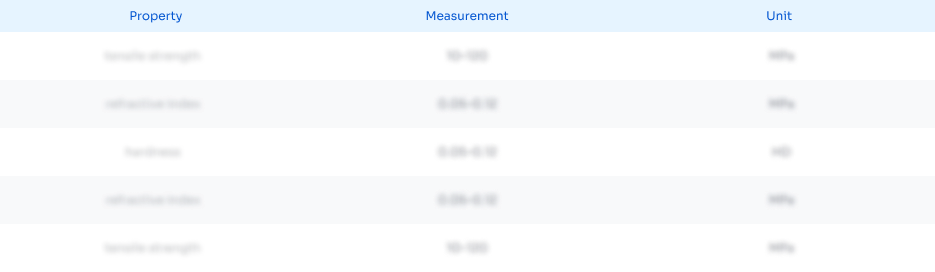
Abstract
Description
Claims
Application Information

- R&D
- Intellectual Property
- Life Sciences
- Materials
- Tech Scout
- Unparalleled Data Quality
- Higher Quality Content
- 60% Fewer Hallucinations
Browse by: Latest US Patents, China's latest patents, Technical Efficacy Thesaurus, Application Domain, Technology Topic, Popular Technical Reports.
© 2025 PatSnap. All rights reserved.Legal|Privacy policy|Modern Slavery Act Transparency Statement|Sitemap|About US| Contact US: help@patsnap.com