A method for in-situ preparation of highly dispersed metal catalysts by growing two-dimensional nanosheets
A two-dimensional nanotechnology for preparing metals, which is applied in metal/metal oxide/metal hydroxide catalysts, chemical instruments and methods, physical/chemical process catalysts, etc. issues such as being effectively protected, achieving the effects of low cost, small scale, and efficient and easy methods
- Summary
- Abstract
- Description
- Claims
- Application Information
AI Technical Summary
Problems solved by technology
Method used
Image
Examples
Embodiment 1
[0024] Dissolve 3.6349g nickel nitrate hexahydrate in 10ml deionized water to prepare salt solution A1, impregnate A1 solution in 7.3363g commercial γ-Al 2 o 3 and ultrasonically disperse for 30 minutes, dry at 120°C for 2 hours, pass through nitrogen protection, place in an ice-water bath, and mechanically stir vigorously; prepare a reducing agent mixture B1 containing 1.8915 g of sodium borohydride, 0.2 g of sodium hydroxide and 25 ml of water . Add the prepared reducing agent mixture B1 dropwise to the above impregnation system with a peristaltic pump. The dropwise addition time is 90 minutes. After the dropwise addition, continue to react for 2 hours to wait for sufficient reduction. Suction filter the reacted product, and then filter it with deionized water and dehydrated ethanol until the filtrate is neutral, then put it into a beaker with 200ml dehydrated ethanol and stir it openly, the stirring speed is 400r / min, and the stirring time 16h, the catalyst precursor of n...
Embodiment 2
[0026] Dissolve 5.0500g of ferric nitrate nonahydrate in 8ml of deionized water to prepare salt solution A, impregnate solution A in 6.1136g of commercial SiO 2 and ultrasonically disperse for 30 minutes, dry at 120°C for 2 hours, pass through nitrogen protection, place in an ice-water bath, and mechanically stir vigorously; prepare a reducing agent mixture B containing 1.8915 g of sodium borohydride, 0.2 g of sodium hydroxide and 25 ml of water . Add the prepared reducing agent mixture B to the above impregnation system dropwise with a peristaltic pump. The dropwise addition time is 90 minutes. After the dropwise addition, continue to react for 2 hours to wait for sufficient reduction. Suction filter the reacted product, and then filter it with deionized water and dehydrated ethanol until the filtrate is neutral, then put it into a beaker with 200ml dehydrated ethanol and stir it openly, the stirring speed is 400r / min, and the stirring time For 16h, the catalyst precursor of...
Embodiment 3
[0028] Dissolve 3.6379g of cobalt nitrate hexahydrate in 28ml of deionized water to prepare salt solution A, impregnate solution A in 4.8911g of commercial TiO 2and ultrasonically disperse for 30 minutes, dry at 120°C for 2 hours, pass through nitrogen protection, place in an ice-water bath, and mechanically stir vigorously; prepare a reducing agent mixture B containing 1.8915 g of sodium borohydride, 0.2 g of sodium hydroxide and 25 ml of water . Add the prepared reducing agent mixture B to the above impregnation system dropwise with a peristaltic pump. The dropwise addition time is 90 minutes. After the dropwise addition, continue to react for 2 hours to wait for sufficient reduction. Suction filter the reacted product, and then filter it with deionized water and dehydrated ethanol until the filtrate is neutral, then put it into a beaker with 200ml dehydrated ethanol and stir it openly, the stirring speed is 400r / min, and the stirring time For 16h, the catalyst precursor of...
PUM
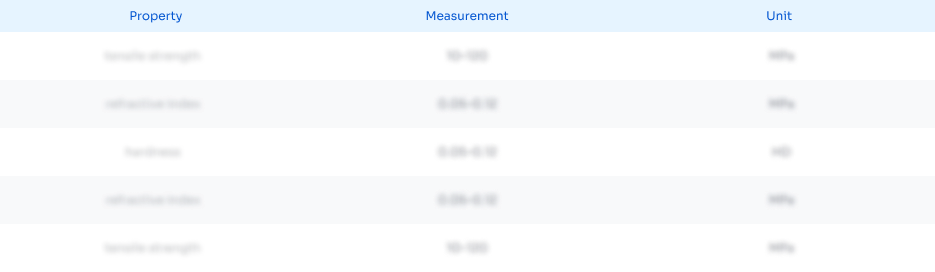
Abstract
Description
Claims
Application Information

- R&D
- Intellectual Property
- Life Sciences
- Materials
- Tech Scout
- Unparalleled Data Quality
- Higher Quality Content
- 60% Fewer Hallucinations
Browse by: Latest US Patents, China's latest patents, Technical Efficacy Thesaurus, Application Domain, Technology Topic, Popular Technical Reports.
© 2025 PatSnap. All rights reserved.Legal|Privacy policy|Modern Slavery Act Transparency Statement|Sitemap|About US| Contact US: help@patsnap.com