A transmission shaft spline full tooth surface grinding residual stress simulation method
A residual stress and simulation method technology, applied in special data processing applications, instruments, calculations, etc., can solve problems such as different processing directions, and achieve the effect of reducing time and economic costs
- Summary
- Abstract
- Description
- Claims
- Application Information
AI Technical Summary
Problems solved by technology
Method used
Image
Examples
Embodiment Construction
[0022] The implementation of the method of the present invention will be described in detail below in conjunction with the accompanying drawings. Although exemplary embodiments of the present disclosure are shown in the drawings, it should be understood that the present disclosure may be embodied in various forms and should not be limited by the embodiments set forth herein. Rather, the embodiments are provided for more thorough understanding of the present disclosure, and for fully conveying the scope of the present disclosure to those skilled in the art. The present invention will be described in detail below with reference to the accompanying drawings and examples.
[0023] The embodiment of the present invention takes a spline tooth on the transmission shaft as an object, maps the grinding residual stress tensor obtained from the simulation analysis of the existing simple grinding process to the entire spline tooth surface node, and realizes grinding based on simple local ...
PUM
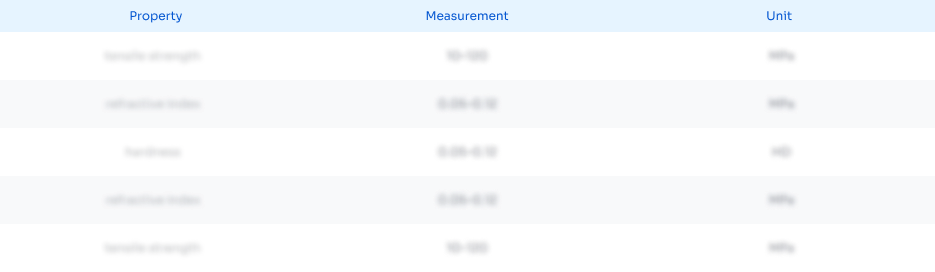
Abstract
Description
Claims
Application Information

- Generate Ideas
- Intellectual Property
- Life Sciences
- Materials
- Tech Scout
- Unparalleled Data Quality
- Higher Quality Content
- 60% Fewer Hallucinations
Browse by: Latest US Patents, China's latest patents, Technical Efficacy Thesaurus, Application Domain, Technology Topic, Popular Technical Reports.
© 2025 PatSnap. All rights reserved.Legal|Privacy policy|Modern Slavery Act Transparency Statement|Sitemap|About US| Contact US: help@patsnap.com